1. Introduction
In the field of metal processing, press brake and metal thickness are two concepts. As a mechanical press, press brake bending machine is mainly responsible for the bending and forming of metal sheets. Metal thickness, that is, the vertical thickness of metal sheets, is a key parameter that affects processes such as bending, cutting, and forming.
Metal thickness is directly related to the selection and bending performance of the brake press. Metals of different thicknesses require press brakes of different models and performances to handle, which will also affect the bending process and final effect. Understanding the significance of common metals and their thickness levels to the process, mastering bending tonnage calculations, process parameters, and on-site solutions are essential to improving the efficiency and quality of metal processing.
This article aims to help manufacturing personnel gain an in-depth understanding of the impact of different metal thicknesses on bending operations, so that they can make more reasonable decisions when selecting and configuring press brakes, thereby improving production efficiency and product quality.
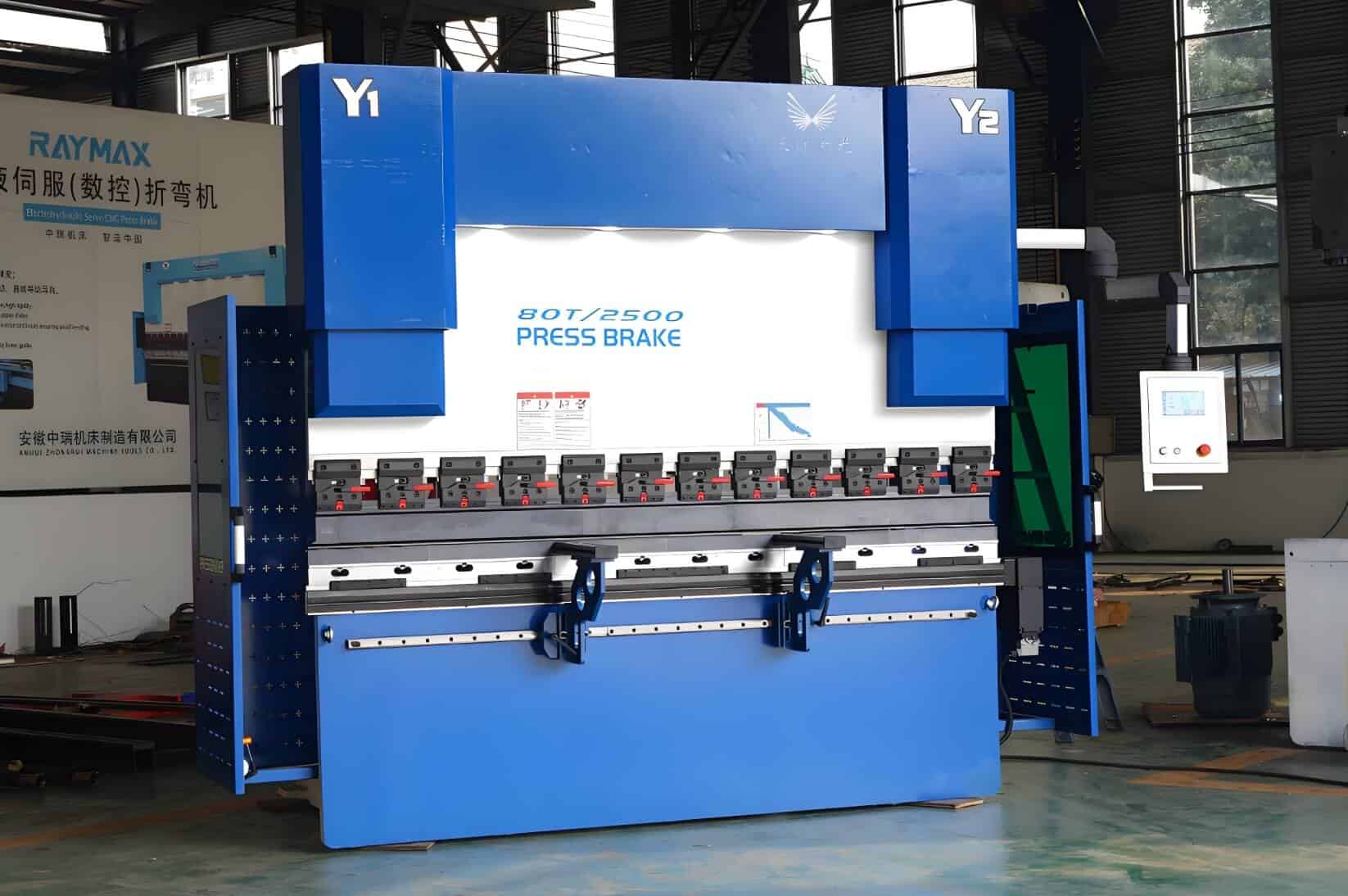
2. Basic knowledge of metal thickness of press brakes
2.1 The importance of metal thickness to the selection of press brakes
Material thickness plays a decisive role in choosing the right brake press and mold. Thicker materials require higher tonnage press brakes. If you choose a low-tonnage brake press, it will not only damage the machine and increase maintenance costs, but also affect the uniform and accurate bending effect of the material.
2.2 Common units of metal thickness (mm and inch)
In the industry, the commonly used units for measuring metal thickness are millimeters (mm) and inches (inch). Millimeters are widely used in most Asian and European factories, while the imperial unit inch is more common in North America. The conversion relationship between them is 1 inch = 25.4 mm. In addition, in addition to feet, the United States also often uses Gauge (American Standard) to indicate metal thickness. In practical applications, these counting units usually need to be converted.
2.3 General classification of metal thickness and its industry standards
2.3.1 Thin plate: refers to the thickness range of 0.5mm – 3mm, such as home appliance housings often use thin plates.
2.3.2 Medium plate: refers to the thickness between 3mm – 10mm, which can be used for mechanical housings.
2.3.3 Thick plate: refers to metal with a thickness of 10mm – 20mm and above, which is often used in heavy machinery, etc. Different
2.3.4 Other thicknesses: JIS, GB, EN, etc. have strict definitions of metal thickness, such as EN 10029, GB/T 709 and other standards. Different metal materials may also have their own thickness classification standards.
3. Common metals and their typical thickness ranges
3.1 Carbon steel
Carbon steel has the largest thickness range among common metals, with a common thickness of 0.5-20mm. Thanks to its large thickness and high hardness, carbon steel is very popular in large-scale manufacturing fields such as automobiles and engineering, and adopts the GB/T709 standard;
3.2 Stainless steel
The general thickness is 0.5-12 mm. This material is thinner than carbon steel, and is very corrosion-resistant and hygienic. It is used in the kitchen, medical, decoration and other industries, which conforms to people’s aesthetics and hygiene. The ASTM A240 standard is used.
3.3 Aluminum plate
Aluminum is lighter than other corrosion-resistant metals, with an average thickness of only 0.5-10mm. Its “small weight” is the only choice for electronic housings, aviation parts, etc. The corresponding standard is GB/T3880.
3.4 Copper
The conventional thickness is 0.5-5mm, and its thermal and electrical conductivity are excellent, and it has a metallic luster, so it is mostly used for conductive parts, decorative parts, etc., and the reference is GB/T2059 standard.
3.5 Standard Sheet Thickness Lookup Chart
Material Name 10833_dd5656-85> |
Available Gauge Thickness, Inch. 10833_ae9f74-63> |
---|---|
Aluminum 2024-T3 10833_4730d2-14> |
0.025” 10833_37c07a-ac> |
Aluminum 5052 H32 10833_40b869-e7> |
0.020”, 0.025”, 0.032”, 0.040”,0.050”, 0.063”, 0.080”, 0.090”, 0.100”, 0.125”, 0.160”, 0.188”, 0.250”, 0.375”, 0.500” 10833_d318d2-1c> |
Aluminum 6061 T6 10833_e9c61d-62> |
0.016”, 0.020”, 0.025”, 0.032”, 0.040”, 0.050”, 0.063”, 0.080”, 0.090”, 0.100”, 0.125”, 0.160”, 0.190”, 0.250”, 0.313”, 0.375”, 0.500”, 0.625”, 0.750”, 0.750”, 0.875”, 1.000” 10833_54beff-3d> |
Aluminum 7075 T6 10833_ea6e0d-05> |
0.025”, 0.032”, .040”, 0.050”, 0.063”, 0.071”, 0.080”, 0.090”, 0.100”, 0.125”, 0.160”, 0.190”, 0.250”, 0.375”, 0.500”, 0.625”, 0.750”, 1.000” 10833_ff76fb-99> |
Aluminum MIC6 10833_70787c-79> |
0.250”, 0.375”, 0.500”, 0.750” 10833_b15f97-9a> |
Pre-Anodized 6061-T6, Black 10833_47a291-ca> |
0.063”, 0.125”, 0.250”, 0.375”, 0.500” 10833_40ddb3-1f> |
Brass 260 10833_2979b5-4f> |
0.005”, 0.010”, 0.016”, 0.020”, 0.025”, 0.032”, 0.040”, 0.050”, 0.063”, 0.080”, 0.093”, 0.125”, 0.188”, 0.250” 10833_a45799-44> |
Brass 353 H02 10833_f2e535-60> |
0.063”, 0.125”, 0.150” 10833_8d4ee1-03> |
Brass 464 H01 10833_e00dee-f5> |
0.032”, 0.040”, 0.063”, 0.080” 10833_2d367b-7b> |
Bearing Bronze 932 M07 10833_e1f489-28> |
0.250” 10833_0f3b8f-4d> |
Bronze 220 H02 10833_35364c-c8> |
0.020”, 0.032”, 0.040”, 0.050”, 0.064”, 0.080”, 0.090”, 0.125” 10833_055773-91> |
Bronze 510 H08 (spring) 10833_068876-50> |
0.005”, 0.008”, 0.010”, 0.016”, 0.020”, 0.032”, 0.040”, 0.050”, 0.064”, 0.090”, 0.125” 10833_5096a5-8c> |
Silicon Bronze 655 10833_40ca38-4f> |
0.063” 10833_a5d552-e9> |
Copper 101, H00 to H01 10833_2d007e-4d> |
0.025”, 0.032”, 0.040”, 0.050”, 0.063” 10833_892d62-05> |
Copper 110, Annealed 10833_968dec-ac> |
0.005”, 0.010”, 0.021”, 0.043”, 0.063”, 0.093”, 0.125” 10833_3bb3b4-f0> |
Copper 110, H01 10833_2baee9-e7> |
0.016” 10833_f8c5f3-8e> |
Copper 110, H02 10833_c44fe1-52> |
0.020”, 0.040”, 0.050”, 0.063”, 0.080”, 0.093”, 0.125”, 0.188”, 0.250” 10833_d603f4-23> |
Nickel 200, annealed 10833_b20883-95> |
0.019”, 0.062” 10833_3c7549-4e> |
Nickel 625, annealed 10833_a02996-c8> |
0.020”, 0.032”, 0.040”, 0.050”, 0.063” 10833_0ad8b3-c9> |
Stainless Steel 17-4 PH, annealed 10833_3a7a1e-0e> |
0.018”, 0.032”, 0.040” 10833_51e5f7-6f> |
Stainless Steel 17-7 shim, hardened 10833_b29afe-50> |
0.004”, 0.005”, 0.010”, 0.020”, 0.031” 10833_0754fc-2e> |
Stainless Steel 301, spring temper 10833_7a0df9-a2> |
0.005”, 0.006”, 0.010”, 0.012”, 0.015”, 0.018”, 0.020”, 0.031”, 0.042”, 0.048”, 0.059” 10833_005c7d-b4> |
Stainless Steel 304 10833_d14c68-2f> |
0.018”, 0.024”, 0.030”, 0.036”, 0.048”, 0.060”, 0.075”, 0.105”, 0.120”, 0.188”, 0.250”, 0.313”, 0.375”, 0.500”, 0.625”, 0.750”, 1.000” 10833_2aa9ed-e0> |
Stainless Steel 304 shim, hardened 10833_3ba18a-99> |
0.005”, 0.006”, 0.010”, 0.012”, 0.015”, 0.020”, 0.025” 10833_326d28-0c> |
Stainless Steel 304, #4 brushed 10833_ca023c-4d> |
0.024”, 0.036”, 0.048”, 0.060”, 0.075”, 0.090”, 0.120”, 0.135”, 0.250”, 0.375”, 0.500”, 0.625” 10833_65b092-63> |
Stainless Steel 316 10833_7fa3db-b9> |
0.018”, 0.024”, 0.030”, 0.036”, 0.048”, 0.060”, 0.075”, 0.105”, 0.120”, 0.135”, 0.188”, 0.250”, 0.313”, 0.375”, 0.500”, 0.625”, 0.750”, 1.000” 10833_5be398-16> |
Stainless Steel 410, annealed 10833_c2bbc7-c1> |
0.250” 10833_bd26df-d9> |
Stainless Steel 430, #3 brushed 10833_27ab80-ff> |
0.035”, 0.046”, 0.060” 10833_9ea21f-13> |
Stainless Steel 440C 10833_33319a-32> |
0.063”, 0.094”, 0.125”, 0.156”, 0.188” 10833_e4f30e-c0> |
Stainless Steel CPM 154 10833_e1c018-88> |
0.063”, 0.094”, 0.125”, 0.156”, 10833_6eb0b7-cd> |
Stainless Steel S30V, annealed 10833_fce3b7-ce> |
0.094”, 0.125”, 0.188”, 0.250” 10833_98d059-6b> |
1075 Spring Steel, annealed 10833_0e4b97-eb> |
0.050”, 0.188” 10833_b220e6-89> |
1075 Spring Steel, Blue Tempered 10833_cf7693-8f> |
0.015” 10833_2c16f6-76> |
1095 Spring Steel, annealed 10833_5f0cd0-01> |
0.015”, 0.025”, 0.035”, 0.050”, 0.063”, 0.083”, 0.125”, 0.188” 10833_f118d7-ac> |
1095 Spring Steel, blue tempered 10833_1ac6fb-04> |
0.005”, 0.008”, 0.010”, 0.015”, 0.020”, 0.025”, 0.030”, 0.035”, 0.042”, 0.050”, 0.063” 10833_4a7a4a-81> |
4130 chrome-moly steel, annealed 10833_131eaa-2f> |
0.032”, 0.040”, 0.050”, 0.063”, 0.080”, 0.100”, 0.125”, 0.160”, 0.190”, 0.250” 10833_afe498-01> |
AR400 Steel, hardened 10833_ed16f5-da> |
0.125”, 0.188”, 0.250”, 0.375”, 0.500” 10833_7dd480-cc> |
AR500 Steel, hardened 10833_086d46-1c> |
0.119”, 0.188”, 0.250”, 0.375”, 0.500”, 0.625”, 0.750” 10833_046f93-31> |
Corten A588 (Weathered) Steel 10833_799004-7d> |
0.060”, 0.075”, 0.100”, 0.120”, 0.135”, 0.188”, 0.250” 10833_5c018a-a9> |
Hot Rolled Steel 1045 10833_49bc0f-18> |
0.250”, 0.375”, 0.500”, 0.625”, 0.750”, 1.000” 10833_ad9a14-26> |
Hot Rolled Steel A569/ASTM A1011 10833_a3e7c4-89> |
0.060”, 0.075”, 0.105”, 0.125”, 0.135” 10833_0afb82-91> |
Steel 1008, zinc-galvanized 10833_2ee558-2b> |
0.024”, 0.033”, 0.048”, 0.060”, 0.075”, 0.100”, 0.120”, 0.135” 10833_00fa44-eb> |
Steel 1018 10833_97e0ed-28> |
0.125”, 0.188”, 0.250”, 0.313”, 0.375”, 0.500”, 0.625”, 0.750”, 0.875”, 1.000” 10833_11db4e-a6> |
Steel 4140, hardened 10833_e6d016-2a> |
0.125”, 0.188”, 0.250”, 0.375”, 0.500” 10833_16d3bf-f8> |
Steel 80CRV2 10833_1a0a21-46> |
0.125”, 0.188” 10833_a57fbe-e8> |
Steel A36 10833_aebb36-e1> |
0.100”, 0.120”, 0.188”, 0.250”, 0.313”, 0.375”, 0.500”, 0.625”, 0.750”, 1.000” 10833_1f3019-7e> |
Steel A36, pickled and oiled 10833_05a833-20> |
0.060”, 0.075”, 0.100”, 0.120”, 0.135”, 0.135”, 0.188”, 0.250”, 0.375”, 0.500” 10833_6f4dbd-39> |
Steel A366/1008 10833_c297aa-63> |
0.024”, 0.030”, 0.036”, 0.048”, 0.060”, 0.075”, 0.090”, 0.105”, 0.125” 10833_72c80e-46> |
Steel A572 Grade 50 10833_02c13e-91> |
0.188”, 0.250”, 0.313”, 0.375”, 0.500” 10833_b5f7ae-a1> |
Steel G90, galvanized 10833_85872a-e5> |
0.022”, 0.024”, 0.033”, 0.048”, 0.060” 10833_83dc60-c0> |
Tool Steel D2, annealed 10833_0ceb9e-0e> |
0.063”, 0.094”, 0.125”, 0.156”, 0.188” 10833_b3154a-f5> |
Tool Steel O1, annealed 10833_70d514-9a> |
0.016”, 0.031”, 0.047”, 0.063”, 0.078”, 0.094”, 0.109”, 0.125”, 0.156”, 0.188”, 0.250”, 0.313”, 0.375”, 0.438”, 0.500” 10833_072eb6-f3> |
Titanium (Grade 2) 10833_d8731b-f8> |
0.035” 10833_0c18e2-a1> |
Titanium 6Al-4V (Grade 5) 10833_1b36ce-fe> |
0.032”, 0.063”, 0.125”, 0.188”, 0.250” 10833_78fdda-9d> |
Sheet thickness lookup chart for sheet cutting or forming processes. These are the standard available thicknesses of the listed material; other thicknesses may be available upon request. RAYMAX uses thickness measurements instead of sheet gauges.
4. How to choose the appropriate metal thickness of the press brake
4.1 The influence of material type on the thickness of the bending metal
Different materials have different characteristics, and their tensile strength, ductility, yield strength and plasticity are different. For example, the yield strength of standard Q235 steel is about 235MPa. For materials, the stronger the characteristics, the greater the required bending force.
Note: Table of tensile strength range of common metallic materials
Material 10833_f33401-ab> |
Tensile strength range (MPa) 10833_f65f2a-89> |
Description 10833_bc843d-09> |
Low carbon steel (mild steel) 10833_bd4001-b5> |
300 – 500 10833_923ddb-bd> |
Common building and structural materials 10833_930bff-19> |
Medium carbon steel 10833_e5c567-66> |
600 – 800 10833_1caed7-87> |
Used for mechanical parts 10833_fe51ae-02> |
High carbon steel 10833_668549-c0> |
800 – 1200 10833_cb6669-50> |
High hardness and strength 10833_c0b889-9d> |
Stainless steel 10833_065bfd-a0> |
520 – 1250 10833_31879d-8f> |
Corrosion-resistant, widely used 10833_88e3bb-34> |
Aluminum alloy 10833_8ee19f-34> |
200 – 600 10833_a4a2fc-d4> |
Lightweight, easy to form 10833_e0cb0b-a2> |
Brass 10833_a59d22-84> |
300 – 900 10833_7a9457-e2> |
Good corrosion resistance 10833_6275c9-b1> |
Titanium alloy 10833_dac900-79> |
700 – 1200 10833_9c6812-21> |
Lightweight and high strength, good corrosion resistance 10833_f3fede-d1> |
Magnesium alloy 10833_5155d5-53> |
200 – 350 10833_ecf9ef-31> |
Extremely light, but low tensile strength 10833_ddca4f-9c> |
4.2 Relationship between metal thickness and bending radius
According to experience, the bending radius should be controlled to 1 to 1.5 times the material thickness, which can ensure that the material is prevented from cracking or damage, thereby ensuring a good folding effect. A larger thickness requires a larger radius. For example, 3mm stainless steel is recommended to be no less than 6mm.
4.3 Tonnage and capacity of the brake press
The tonnage of the brake press determines the upper limit of the force that can be applied, which directly determines the maximum metal thickness that can be bent. The general tonnage calculation formula is:
Tonnage=L×T×(YieldStrength×K)Tonnage=L×T×(YieldStrength×K).
Where L is the bending length, T is the metal thickness, and K is determined according to the material characteristics. It is not that the larger the tonnage, the better. To ensure the accuracy of large and thick parts, the tonnage of the brake press bending machine is generally required to be proportional to the thickness.
4.4 Die Selection and V-groove Specifications
V-grooves are prone to cracking if they are too narrow, have large rebound if they are too wide, and are not wear-resistant for hard materials. When choosing to use V-grooves to process materials, it is important to control the width of the V-groove to be approximately 8 to 10 times the thickness of the metal, and the die length should not be less than the maximum bending length of the workpiece.
Note: V-Die Sizing Table (Using Rule of Eight)
Width of V-Die Opening | Thickness of Metal | |||||||||||||||||||||
26Ga .018″ | 24Ga .024″ | 22Ga .030″ | 20Ga .036″ | 18Ga .048″ | 16Ga .060″ | 14Ga .075″ | 13Ga .090″ | 12Ga .105″ | 11Ga .120″ | 10Ga .135″ | 9 Ga .149″ | 7Ga .187″ | 1/4 .250″ | 5/16 .313″ | 3/8 .375″ | 7/16 .437 | 1/2 .500″ | 5/8 .625″ | 3/4 .750″ | 7/8 .875″ | 1″ | |
1/8″ | 1.2 | 2.1 | 3.6 | . | . | . | . | . | . | . | . | . | . | . | . | . | . | . | Need Die Opening 10X material thickness | |||
3/16″ | 0.8 | 1.4 | 4.1 | . | . | . | . | . | . | . | . | . | . | . | . | . | . | . | ||||
1/4″ | 0.5 | 1.1 | 1.8 | 2.9 | 5.4 | . | . | . | . | . | . | . | . | . | . | . | . | . | . | . | . | . |
5/16″ | . | 0.7 | 1.4 | 2.2 | 4.0 | 7.0 | . | . | . | . | . | . | . | . | . | . | . | . | . | . | . | . |
3/8″ | . | . | 1.0 | 1.7 | 2.9 | 5.6 | 8.8 | . | . | . | . | . | . | . | . | . | . | . | . | . | . | . |
1/2″ | . | . | . | 1.2 | 2.2 | 3.6 | 10.0 | . | . | . | . | . | . | . | . | . | . | . | . | . | . | . |
5/8″ | . | . | . | . | 1.6 | 2.7 | 4.5 | 6.8 | 10.1 | . | . | . | . | . | . | . | . | . | . | . | . | . |
3/4″ | . | . | . | . | 1.3 | 2.2 | 3.4 | 5.4 | 7.4 | 10.5 | . | . | . | . | . | . | . | . | . | . | . | . |
7/8″ | . | . | . | . | . | 1.7 | 3.0 | 4.3 | 6.3 | 8.8 | 11.3 | . | . | . | . | . | . | . | . | . | . | . |
1″ | . | . | . | . | . | 1.4 | 2.5 | 3.7 | 5.4 | 7.2 | 9.6 | 13.1 | . | . | . | . | . | . | . | . | . | . |
1 1/8″ | . | . | . | . | . | . | 2.1 | 3.3 | 4.4 | 6.2 | 8.4 | 11.9 | 16.4 | . | . | . | . | . | . | . | . | . |
1 1/4″ | . | . | . | . | . | . | 1.7 | 2.9 | 4.0 | 5.4 | 7.0 | 9.0 | 14.0 | 28.8 | . | . | . | . | . | . | . | . |
1 1/2″ | . | . | . | . | . | . | . | . | 3.2 | 4.3 | 5.6 | 6.7 | 11.2 | 22.0 | 38.0 | . | . | . | . | . | . | . |
2″ | . | . | . | . | . | . | . | . | . | 3.2 | 4.1 | 5.2 | 7.6 | 15.3 | 26.0 | 41.0 | . | . | . | . | . | . |
2 1/2″ | . | . | . | . | . | . | . | . | . | . | 2.4 | 3.5 | 5.8 | 11.5 | 19.2 | 29.9 | 45.2 | . | . | . | . | . |
3″ | . | . | . | . | . | . | . | . | . | . | . | 2.2 | 4.5 | 9.1 | 16.0 | 24.0 | 35.0 | 47.9 | . | . | . | . |
3 1/2″ | . | . | . | . | . | . | . | . | . | . | . | . | . | 7.5 | 12.5 | 19.4 | 28.0 | 39.0 | 69.5 | . | . | . |
4″ | . | . | . | . | . | . | . | . | . | . | . | . | . | 6.2 | 10.6 | 16.0 | 24.0 | 33.1 | 58.0 | 92.0 | . | . |
5″ | . | . | . | . | . | . | . | . | . | . | . | . | . | . | 7.6 | 12.3 | 17.0 | 24.0 | 42.2 | 69.0 | 104.0 | . |
6″ | . | . | . | . | . | . | . | . | . | . | . | . | . | . | . | 9.3 | 14.6 | 19.0 | 32.4 | 52.2 | 80.0 | 112.2 |
7″ | . | . | . | . | . | . | . | . | . | . | . | . | . | . | . | . | 11.1 | 15.6 | 26.0 | 42.2 | 63.0 | 90.2 |
8″ | . | . | . | . | . | . | . | . | . | . | . | . | . | . | . | . | . | 12.7 | 23.0 | 36.0 | 52.5 | 76.0 |
10″ | . | . | . | . | . | . | . | . | . | . | . | . | . | . | . | . | . | . | 16.5 | 27.0 | 39.4 | 56.2 |
12″ | . | . | . | . | . | . | . | . | . | . | . | . | . | . | . | . | . | . | . | 21.0 | 31.2 | 44.0 |
4.5 Recommended Metal Thickness Range
To maintain the machine, ensure that the actual bending thickness of the material should not exceed 80% of the equipment’s calibrated limit before processing. Each brake press has its recommended metal thickness range.
4.5.1 Manual brake press: Usually used to process thinner materials, the recommended metal thickness range is 18 (0.0478 inches) to 10 (0.135 inches).
4.5.2 Hydraulic brake press: more powerful and more efficient, the metal thickness range that can be processed is generally from 24 gauge (0.0239 inches) to 1/2 inch (0.500 inches) or even thicker;
4.5.3 CNC brake press: precise control and high degree of automation, the recommended processing thickness range is usually from 24 gauge (0.0239 inches) to several inches.
5. Calculation of metal thickness and bending tonnage
5.1 Bending tonnage calculation formula
Calculating the relationship between metal thickness and bending tonnage is a key step for processing materials.
5.1.1 P = 650×S²×L/V can be used for calculation. Where P is the nominal force of the press brake bending machine(KN), S is the thickness of the folded plate (mm), L is the width of the folded plate (m), and V is the lower die opening width (mm). The lower die opening width is generally 8-10 times the thickness of the folded plate.
5.1.2 P = 1.42×σ×t²×L / (1000×V) can be used, where P is the bending force (tons), σ is the material tensile strength (N/mm²), t is the metal thickness (mm), L is the bending length (mm), and V is the V-groove width (mm).
5.1.3 Tonnage = (L×W×T×Y) / 0.785 can be used, where L is the bending length, W is the material width, T is the metal thickness, and Y is the yield strength of the material.
5.2 Quick Reference Table (Mild Steel):
Thickness (mm) 10833_d46051-16> |
V-Opening (mm) 10833_33c3e6-23> |
Tonnage per meter 10833_09166d-da> |
---|---|---|
6 mm 10833_7307ad-e8> |
48 mm 10833_39a1d6-9f> |
~43 tons 10833_8a347d-58> |
8 mm 10833_ccc076-ca> |
64 mm 10833_4b125d-3a> |
~57.5 tons 10833_e75e01-09> |
10 mm 10833_3c3cc8-32> |
80 mm 10833_242c67-40> |
~71.9 tons 10833_2bf333-28> |
12 mm 10833_6a65af-75> |
96 mm 10833_9d1f96-db> |
~86 tons 10833_36c8d7-72> |
6. Common problems and solutions when bending metals of different thicknesses
6.1 Bending angle compensation method
During the bending process, the bending angle of thick plates may be difficult to operate due to large springback. At this time, it is necessary to use electronic measurement tools to optimize the angle, and use pressure compensation, angle compensation devices, or take over-bending treatment (the pre-bending angle is 2-4° smaller than the target). With the development of press brakes, modern press brakes bending machine are more fully equipped with laser or mechanical angle detection closed-loop systems, deformation measurement modules, and dynamic pressure adjustment.
6.2 Practical strategies for adjusting pressure and speed
Thin plates and thick plates have different properties. Reasonable adjustment of pressure and speed can achieve the best effect and avoid deformation and cracks. Thin plates should appropriately reduce pressure and speed to reduce wrinkles and surface indentations; thick plates should be bent in sections multiple times to prevent material cracking.
6.3 Common problems: overbending, rebound, cracking, deformation, etc.
6.3.1 Overbending: The degree of bending exceeds the specified range, which may be caused by the die hole being too small or the pressure being too high. It can be solved by enlarging the V-groove or bending in sections.
6.3.2 Rebound: When the pressure is released, the material will deform into its original state, which can be solved by increasing the bending angle or extending the holding time.
6.3.3 Cracking: It may be caused by poor material toughness, too small R angle or too high pressure. It is necessary to increase the R angle or reduce the pressure;
6.3.4 Deformation: Uneven bending leads to uneven material shape. Support devices can be added in sections.
6.4 Preventive and corrective measures to improve bending quality
As an important part of factory production, the factory unit should calibrate the mold regularly and try to use imported high-strength mold steel to ensure stable pressure and smooth oil return of the hydraulic system. Relevant maintenance personnel must regularly check the mold wear and keep the mold surface smooth and clean. With the development of maintenance and prevention technology, more new technologies such as CNC compensation mechanism, intelligent angle monitoring, pressure sensor, etc. can be put into use.
7. Conclusion
The selection of metal thickness and the configuration of the brake press are key links in the metal processing process. When selecting equipment, it is necessary not only to consider a certain margin for metal thickness, but also to consider that different materials must match different parameters.
It is recommended that manufacturing personnel fully combine actual needs to choose suitable manufacturers and services. In this regard, Raymax can provide one-stop project consultation and automation upgrade suggestions for various sheet metal thickness applications. If you have relevant needs, please contact us for professional advice and solutions.
8. FAQ
8.1 What materials can be bent with a press brake?
There are many objects to be bent, including low carbon steel, stainless steel, high strength steel, aluminum alloy (such as 6061 and 5052), copper, brass, titanium and galvanized steel.
8.2 Can the nominal maximum thickness of the press brake bending machine be used at full load for a long time?
Theoretically, it is best not to exceed 80% of the nominal thickness, otherwise the equipment will be easily damaged.
Further Reading
Press Brake Tonnage Explained: Learn How to Calculate for Optimal Performance
What Is a Sheet Metal Press Brake Machine? Working Principles, Bending Techniques & Buying Guide
Top 10 Fiber Laser Cutting Machine Manufacturers of 2025
An Overview of Electric Press Brake Machines and Purchasing Tips
Everything You Need to Know About Press Brake Fundamentals
10 Press Brake Bending Problems and How to Fix Them in Sheet Metal
Press Brake Software: Basics, Implementation, Examples & Selection Guide
Press brake tooling Complete Guide: Pictures and text both profuse, understood at one look!
CNC Press Brake Axis: Mastering Configurations from 2-Axis to 8+1 for Pro Results
Metal Laser Cutting Machine: Buyer’s Ultimate Guide to Costs, Types & Quality Factors
Definition, working principle and selection guide of hybrid press brake
The Golden Rule: How to Operate a CNC Press Brake Correctly
Post Your Review
Share Your Thoughts And Feelings With Others
Hello, Customers!
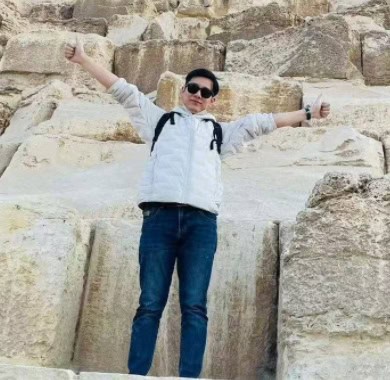
Author introduction
我叫Francis Pan,是RAYMAX的外贸经理。我从事金属制造和数控机械领域已有10多年。欢迎联系我们,我非常乐意为您提供最好的服务和产品。
邮箱: [email protected] | 微信: 13645551070
Top Guidelines
- Press Brake Air Bending: Guide to Principles, Calculations & Best Practices
- What Materials Can a Fiber Laser Cut? A Practical Handbook of Metals, Non-Metals & Limitations
- What is a Fiber Laser Cutting Machine? The Ultimate Guide for 2025
- What is Laser Cutting Machine? The Ultimate Guide for 2025
- Top 10 Fiber Laser Cutting Machine Manufacturers of 2025
- Press Brake Buyers Guide: Expert Tips to Select, Compare, and Buy with Confidence
- Hydraulic Press Brake Troubleshooting: The Ultimate Guide to Fix Common Problems
- Press Brake Radius Mastery: Inside/Outside Radius, 8× Rule, and Real-World Tips
- Press Brake Bending Basics: Everything You Need to Know for Efficient Bending
- Everything You Need to Know About Press Brake Fundamentals