1. Introduction
Press brake bending machine is a widely used equipment in metal processing industry. It uses pressure to bend metal plate into the required shape. The correct use of press brake die can improve the production efficiency of brake press bending machine and play a key role in the quality and durability of finished products. Next, this article will explain in detail what is brake press die, so that you can have a certain understanding of brake press die.
2. What is Press Brake Dies?
The die is a hollow tool placed under the workpiece, made of high-strength material. It absorbs all the force applied by the punch, can support the material processing, guide it to bend, and ensure the accuracy of the bending process. The die and the punch that applies force together form a bending die system.
3. Types of press brake dies
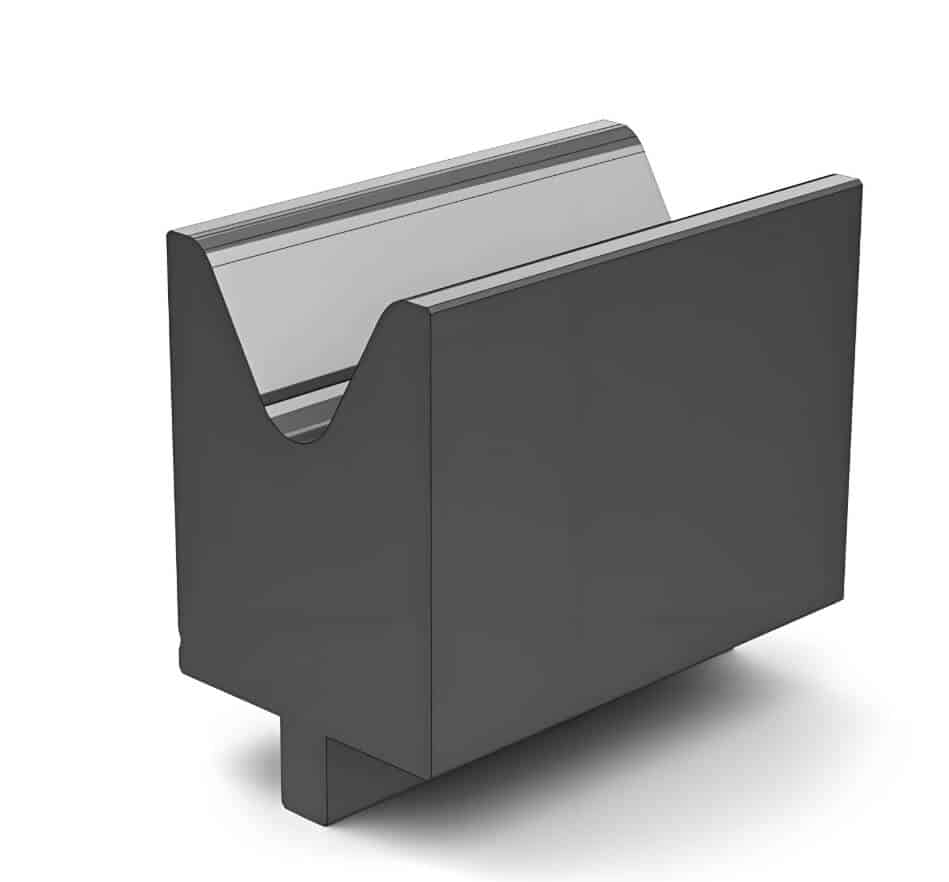
3.1 Single V-type die head
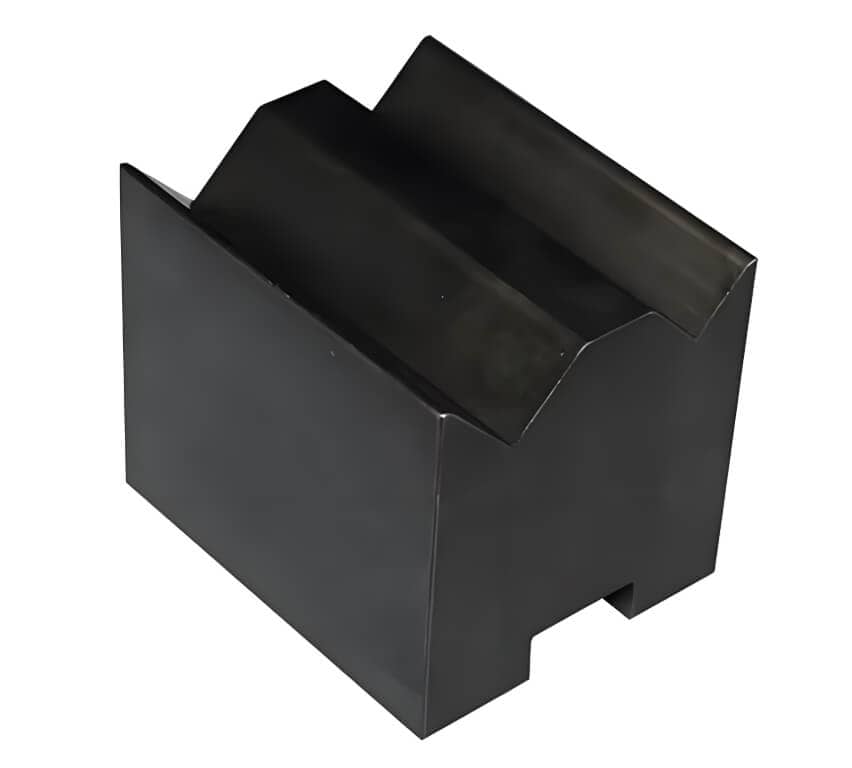
3.2 Bidirectional self-centering V-type die
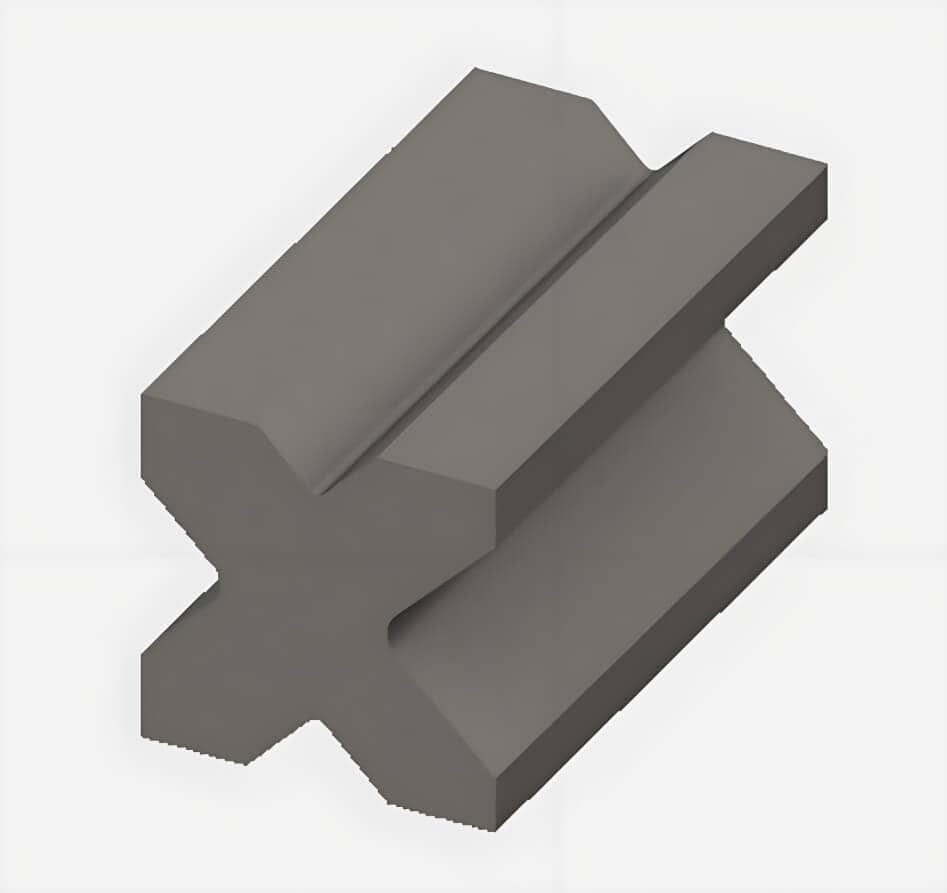
3.3 Multi-V die
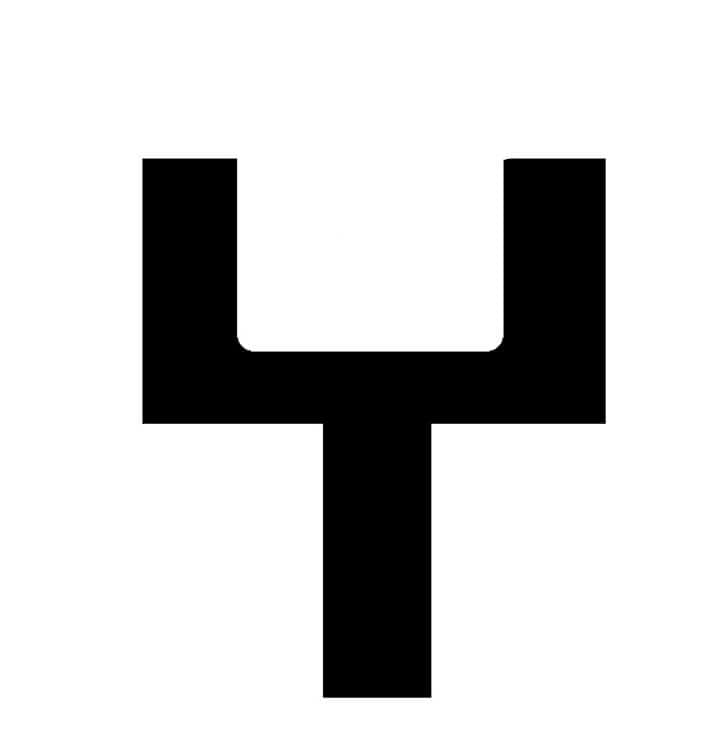
3.4 U-shaped die
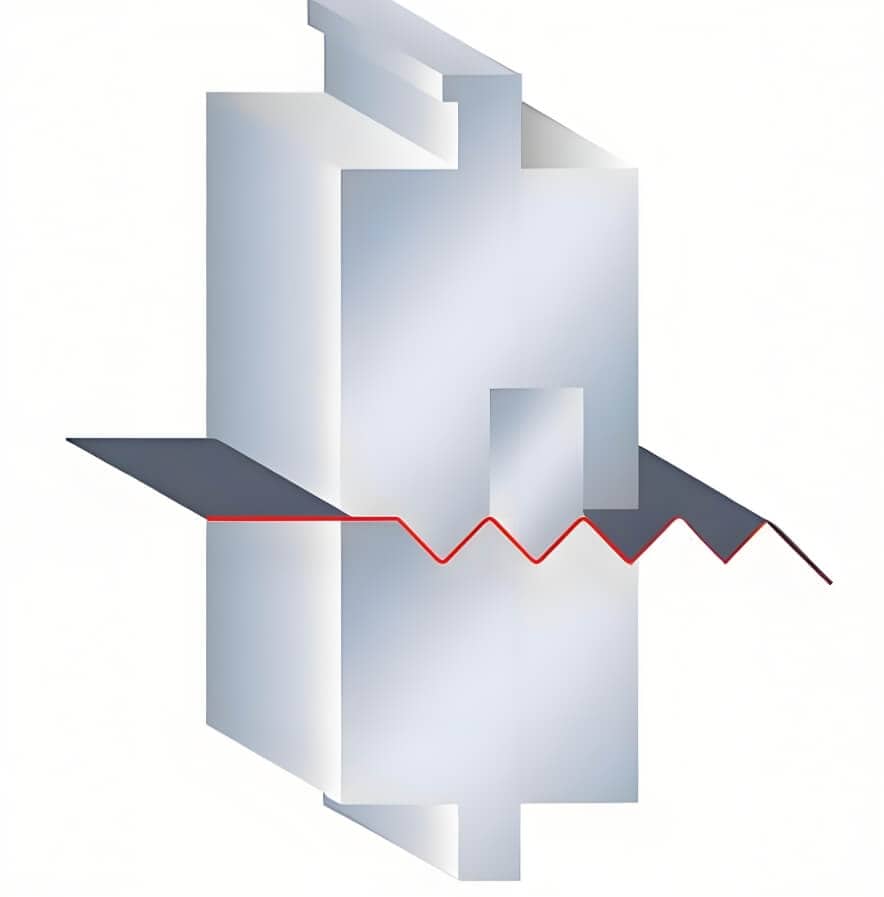
3.5 Corrugated die
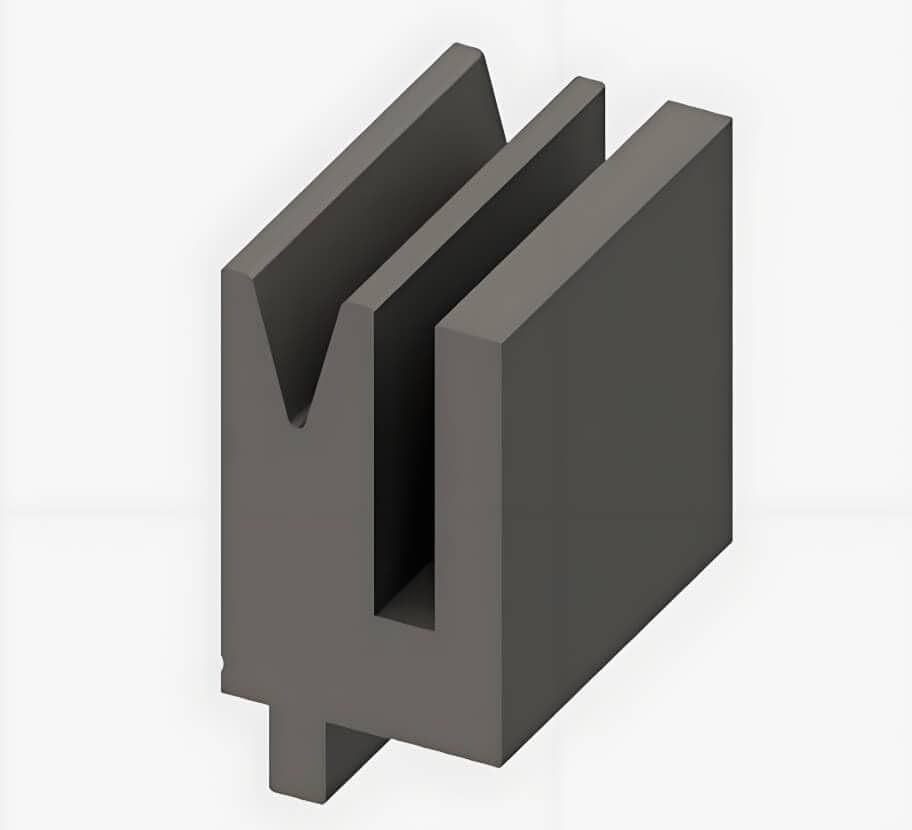
3.6 Flattening and curling dies
3.7 Special custom dies
4. Suitable press brake die selection rules
4.1 V-shaped opening and material radius
The same type of metal plate can choose a variety of V-shaped die opening sizes, but the V-shaped die opening size should not be too large or too small. Too large will cause the bending shape to be loose, and too small will cause tensile deformation and material loss.
4.2 Bending materials
Different materials are bent, and different dies are used. The thickness of the material determines the opening, bending angle, and bending radius of the applicable die. The length of the material determines the number of applicable dies. The tensile strength of the material determines the length of the die used.
4.3 8 rule
The eight-point rule stipulates that the width of the V-shaped opening = material thickness × 8. But this rule is not absolute. It should be judged according to the specific situation. For example, thicker plates sometimes require a V-shaped opening that is ten times larger than their thickness to prevent cracking.
4.4 V-shaped opening affects the radius of the bending length
Generally speaking, the inner radius of the material matches the V-shaped opening. The V-shaped opening affects the radius of the bending length: when the aperture of the V-shaped die increases, the inner radius of the metal sheet will also increase.
4.5 Minimum strength of the leg or flange
During the bending process, the length of the leg plays an important role. If the leg length does not meet the requirements, the flange will fall into the V-shaped opening, making the bending result inaccurate. In traditional V-shaped dies, the minimum leg should be 70% of the V-shaped wide mouth. In acute-angle dies, the minimum leg should be 110% or even higher of the V-shaped wide mouth.
5. Materials for manufacturing the press brake die
The punch and die bear most of the force generated by the brake press bending machine. Therefore, high-strength hardened steel, special grade steel, and some aluminum steel can be selected to manufacture the brake press die. Different materials also have different effects on the performance of the die. For example, steel dies have strong impact resistance, while aluminum dies are light and corrosion-resistant.
Related technical reading : Definition of press brake tool material
6. Maintenance and care of the brake press die
6.1 Daily inspection items
Regularly and carefully check whether the surface of the press brake bending machine is worn and keep the groove clean
6.2 Common damage types and analysis
6.3 How to extend the life of the die
6.4 Common problem handling methods
Minor wear of the die should be repaired in time, and severe wear requires replacement of equipment or calibration.
7. Development trend of brake press die
Under the requirements of the market, die design and manufacturing are constantly improving. From the latest manufacturing process and die materials, the wear resistance and precision of today’s dies are getting higher and higher. At the same time, the application trends of the new generation of press brake die, such as rapid die change and automated die, have improved the production efficiency of bending operations.
8. Summary
Press brake die affects all aspects of industrial production, plays an important role in production efficiency and product quality, and is the core of the bending forming process. From this point of view, choosing a suitable brake press die supplier is also very important. If you want to know more, please consult Raymax to get a professional press brake die solution.
Further Reading
The Golden Rule: How to Operate a CNC Press Brake Correctly
Proper setup steps for Press brakes and analysis of common calibration issues
Definition of press brake tool material
Press Brake Buyers Guide: Expert Tips to Select, Compare, and Buy with Confidence
The Ultimate Guide to Press Brake Safety Devices and Guidelines for 2025
The Ultimate Guide to Press Brake Metal Thickness
Choose the Right Deflection Compensation System for Accurate Bending of Long Workpieces!
How to Use a Press Brake Machine for Precise Bending: Essential Settings, Tools & Tuning
Quickly choose the right laser cutting machine ultimate guide
The top 10 best press brake manufacturers in the world in 2025
Press Brake Radius Mastery: Inside/Outside Radius, 8× Rule, and Real-World Tips
CNC Laser Cutting Machines Comparison:CO₂ vs. Fiber vs. Diode
Post Your Review
Share Your Thoughts And Feelings With Others
Hello, Customers!
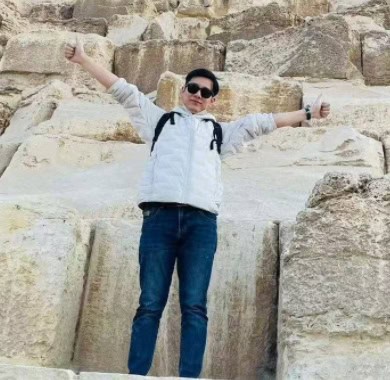
Author introduction
我叫Francis Pan,是RAYMAX的外贸经理。我从事金属制造和数控机械领域已有10多年。欢迎联系我们,我非常乐意为您提供最好的服务和产品。
邮箱: [email protected] | 微信: 13645551070
Top Guidelines
- Press Brake Air Bending: Guide to Principles, Calculations & Best Practices
- What Materials Can a Fiber Laser Cut? A Practical Handbook of Metals, Non-Metals & Limitations
- What is a Fiber Laser Cutting Machine? The Ultimate Guide for 2025
- What is Laser Cutting Machine? The Ultimate Guide for 2025
- Top 10 Fiber Laser Cutting Machine Manufacturers of 2025
- Press Brake Buyers Guide: Expert Tips to Select, Compare, and Buy with Confidence
- Hydraulic Press Brake Troubleshooting: The Ultimate Guide to Fix Common Problems
- Press Brake Radius Mastery: Inside/Outside Radius, 8× Rule, and Real-World Tips
- Press Brake Bending Basics: Everything You Need to Know for Efficient Bending
- Everything You Need to Know About Press Brake Fundamentals