1. Introduction
1.1 The status of hydraulic press brake in metal processing
In the development of today’s industrial manufacturing industry, hydraulic press brake bending machine is an indispensable tool for manufacturing various metal products. In this article, we will explore the definition, main components, working principle, bending process, application, maintenance and safety of hydraulic press brake. The important reasons for choosing hydraulic brake press include its high precision, high efficiency and low maintenance requirements, making it one of the indispensable tools in modern manufacturing industry. Compared with ordinary press brakes, hydraulic brake press can provide high-precision and high-efficiency processing bending for a variety of materials such as thick plates, stainless steel and aluminum, so it is favored by many manufacturing companies.
1.2 Important reasons for choosing hydraulic press brake
The hydraulic press brake bending machine adopts an all-steel welded structure with excellent mechanical strength to ensure stability and reliability during high-intensity processing. By using advanced CNC system, operators can easily set bending parameters, change complex to simple automated operation, and have the function of self-diagnosis of faults to ensure the continuous and stable operation of the equipment. Combining the efficient hydraulic system with the CNC system not only improves the processing efficiency, but also reduces the labor intensity and production costs.
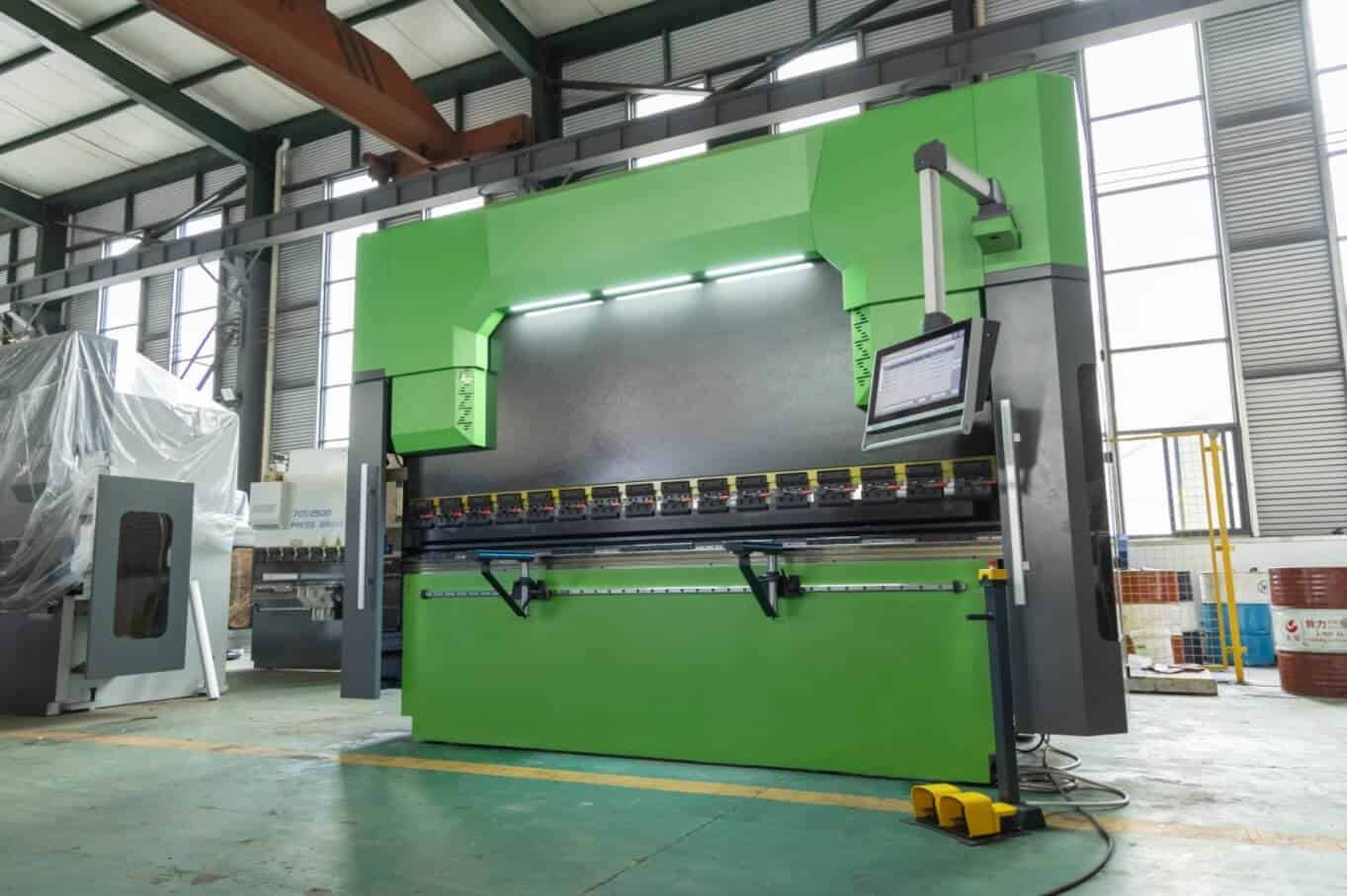
2. What is a hydraulic brake press
2.1 Definition of a hydraulic brake press
A hydraulic press brake bending machine is a mechanical device that uses a hydraulic system to bend metal materials. Compared with mechanical and electric press brakes, hydraulic press brakes provide greater operating flexibility and more consistent pressure, and are suitable for processing various types of thick steel, stainless steel and aluminum. It has a wide range of work and can meet precise processing needs.
2.2 The difference between ordinary press brakes and hydraulic press brakes
Ordinary press brakes bending machine:
Ordinary press brakes rely on manual adjustment of stroke, pressure and stopper position, and the operating accuracy is greatly affected by the worker’s experience. And the repetition accuracy is low, it is difficult to ensure the angle consistency of large-scale products, and it is easily affected by mechanical clearance and elastic deformation.
CNC brake press bending machine:
The hydraulic brake press not only has precise and stable operation, good synchronization performance, high bending accuracy, and high slider repetition positioning accuracy. And according to customer needs, the rear baffle mechanism can use a rear baffle shaft material with better functions.
The hydraulic system adopts an integrated control system to reduce pipeline installation, avoid oil leakage, ensure the working stability of the machine, and make the appearance more scientific and beautiful.
In addition, it is equipped with a hydraulic deflection automatic compensation mechanism to eliminate the influence of slider deformation on the quality of the workpiece. The CNC system automatically adjusts the compensation amount, and the operation is simple and accurate.
Raymax brand high-quality and affordable 30T – 2000T, 4 foot ~ 26 foot hydraulic press brake bending machines are available for online purchase in our inventory store. Please visit: Stock press brake machines For Sale
3. Main components of hydraulic press brake
4. Working principle of hydraulic press brake
The working principle of the press brake is mainly to place the metal material on the workbench and then use the pressure and bending mechanism of the machine to bend the material.
4.1 The flow process of hydraulic oil through the pump and valve
The hydraulic press brake bending machine operates by the force applied by hydraulic oil and controls the accuracy through modern computer technology.
When the operator starts the bending process, the hydraulic pump drives the hydraulic oil to generate pressure. The hydraulic oil drives the hydraulic cylinder through the hydraulic system, causing the punch to move vertically.
The punch then applies force to the metal sheet and presses it into the desired shape through the die.
The operator can control the speed, position and bending force through the computer control system to ensure high-quality bending.

4.2 How hydraulics achieve bending in a brake press
When the operator first places the metal sheet on the workbench, the back gauge clamps the material, and then the operator steps on the pedal or starts the press brake through the controller, the operator controls the hydraulic pressure to pass the punch through the die and then lower it to the predetermined position, thus forming the bending process.
4.3 Stages of the bending cycle
4.4 How to set the bending parameters through the control system
The operator inputs the required bending angle, plate thickness, length, slider stroke, bending depth and other parameters through the CNC system. The 3D diagram of the bending can be seen on the controller, so that the shape after bending can be known more accurately.
5. Bending process of hydraulic press brake
1. Place the material to be bent on the front support arm of the bending.
2. Set the parameters on the controller and replace the required mold and adjust it.
3. The worker starts the pedal of the brake press to complete the entire bending process.
4. Under the action of the upper and lower molds, the workpiece is bent to the set angle to achieve the effect of workpiece forming.
5. After the bending is completed, the finished product is taken out and quality inspection is carried out.
6. Advantages of hydraulic press brake
6.1 Energy and efficiency comparison
The high-pressure system of the press brake reduces ineffective energy consumption through precise oil control, which saves 30%-50% energy compared with traditional equipment, and has higher stability than traditional equipment. Full automation makes efficiency higher.
6.2 Good stability and high repeatability
Due to precise servo motor control, hydraulic brake press bending machine provides higher precision and consistent bending, and can be suitable for large-scale mass production.
6.3 Flexible operation and easy automation
By adjusting the parameters of the hydraulic system, various angles and customized shapes are supported.
6.4 Excellent precision
The control accuracy of the CNC control system reaches ±0.5°, realizing complex parts and high-requirement repetitive work.
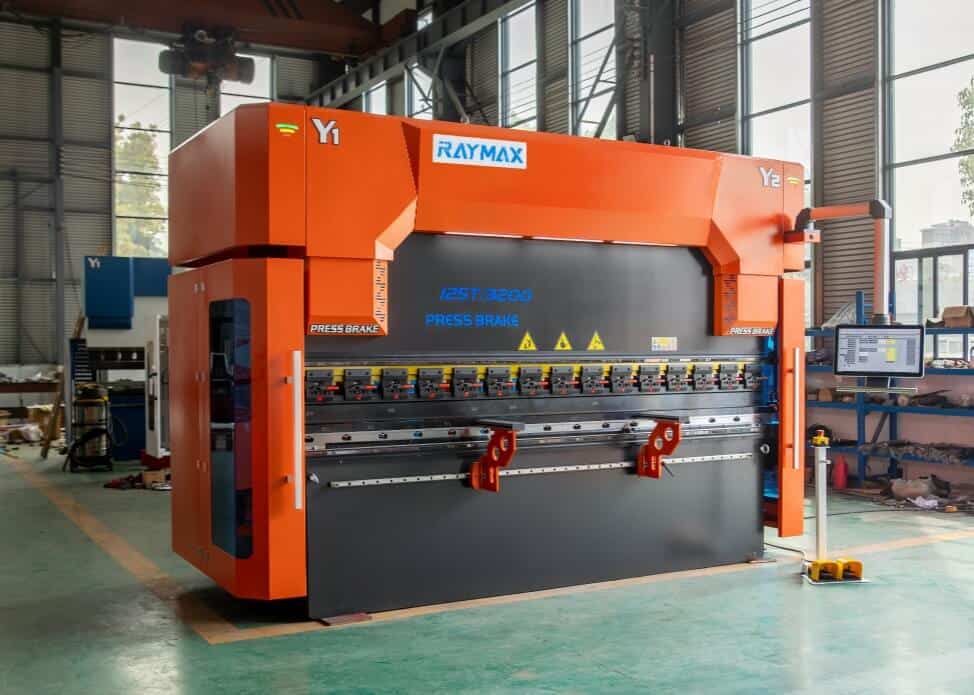
7. Application field
Hydraulic press brake bending machine is widely used in metal sheet processing in the field of industrial machinery, which can meet the use needs of different industries and process into the required shape. Its precision and operating efficiency are indispensable in different fields such as automobiles, aerospace, and construction.
Automobile field: used in the forming and bending of chassis parts, automobile shells, engines, etc.
Aerospace field: used in aircraft wings, fuselages, internal parts, dashboards, etc.
Construction industry: steel bars, bridges, metal roofs, vents, drainage systems, etc.
Manufacturing industry: bent pipes, metal furniture frames, metal cabinets, etc.
8. Maintenance and safety considerations
In order to ensure the service life of the press brake, we need to perform regular maintenance, so what should we do?
We need to check and open the hydraulic oil regularly, observe whether the hydraulic system is kept clean, replace the hydraulic oil on time, and prevent hydraulic oil leakage.
Check whether the machine is damaged, whether there is a problem with the line, whether the motor has a fault, and observe the pressure, oil temperature, abnormal movement, etc. of the hydraulic system.
For the safety of the machine, the steps of the safe operation manual should be strictly followed step by step to ensure that the operator has been trained and the operation is completely problem-free before starting to avoid accidents.
9. Conclusion
Hydraulic press brake plays a pivotal role in the industrial manufacturing industry. It not only makes metal processing more efficient and high-precision, but also more environmentally friendly and energy-saving. Whether in other fields such as automobiles and construction, it plays a particularly important role, thereby promoting the development of the automation era. Through continuous technological innovation, hydraulic press brakes are becoming more and more important.
Further Reading
Definition of press brake tool material
What Materials Can a Fiber Laser Cut? A Practical Handbook of Metals, Non-Metals & Limitations
Ultimate Guide to Hydraulic Press Brake Maintenance: Top Tools, Schedules & Expert Tips
Press Brake Bending Basics: Everything You Need to Know for Efficient Bending
Press Brake Buyers Guide: Expert Tips to Select, Compare, and Buy with Confidence
An Overview of Electric Press Brake Machines and Purchasing Tips
What is a Fiber Laser Cutting Machine? The Ultimate Guide for 2025
Definition, working principle and selection guide of hybrid press brake
Laser Cutting Machine application Explained: Top Materials, Applications & Safety Tips Unveiled
How to Choose a Press Brake Control System? Function, Brand & Buying Guide (Including Delem/ESA)
Proper setup steps for Press brakes and analysis of common calibration issues
Press Brake Radius Mastery: Inside/Outside Radius, 8× Rule, and Real-World Tips
Post Your Review
Share Your Thoughts And Feelings With Others
Hello, Customers!
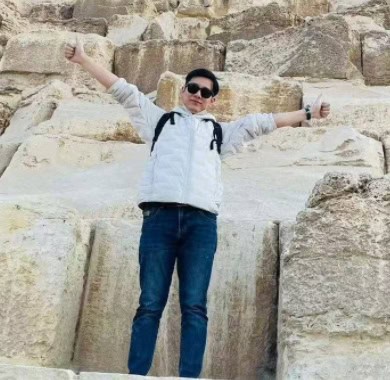
Author introduction
我叫Francis Pan,是RAYMAX的外贸经理。我从事金属制造和数控机械领域已有10多年。欢迎联系我们,我非常乐意为您提供最好的服务和产品。
邮箱: [email protected] | 微信: 13645551070
Top Guidelines
- Press Brake Air Bending: Guide to Principles, Calculations & Best Practices
- What Materials Can a Fiber Laser Cut? A Practical Handbook of Metals, Non-Metals & Limitations
- What is a Fiber Laser Cutting Machine? The Ultimate Guide for 2025
- What is Laser Cutting Machine? The Ultimate Guide for 2025
- Top 10 Fiber Laser Cutting Machine Manufacturers of 2025
- Press Brake Buyers Guide: Expert Tips to Select, Compare, and Buy with Confidence
- Hydraulic Press Brake Troubleshooting: The Ultimate Guide to Fix Common Problems
- Press Brake Radius Mastery: Inside/Outside Radius, 8× Rule, and Real-World Tips
- Press Brake Bending Basics: Everything You Need to Know for Efficient Bending
- Everything You Need to Know About Press Brake Fundamentals