1. Introduction
Press brakes are widely used in aerospace, automobile, construction, parts manufacturing and other industries. Press brakes may encounter different bending problems when bending sheet metal, which is usually caused by a series of factors such as the type of processing materials, different process technologies, equipment accuracy, and improper operation of workers. Therefore, this article will show some common bending problems and their solutions to help customers improve production efficiency and product accuracy.
2. 10 common bending problems
Below we will introduce 10 common types of bending problems and provide solutions for each.
2.1 Springback
Because materials such as metals are elastic, after bending gives pressure to the metal, the metal material will resist bending, resulting in the material returning to its original shape or the actual bending angle being inconsistent with the theoretical angle. There are many reasons for springback, and different processing materials, bending thickness, range, or mold size used may cause springback.
Solutions:
Note: The models and specific parameters of the mainstream CNC numerical control systems for press brake bending machines in the market can be referred to: Press Brake Control System
2.2 Bulging or unevenness
During the bending process, due to different material thickness, loose clamps on the mold, uneven pressure applied by the mold, etc., the bent workpiece may bulge or sink or twist in the middle, thus causing deformation.
Solution:
2.3 Indentation
Rough mold surface or insufficient hardness will cause creases during the bending process, thereby affecting the aesthetics and functionality of the workpiece.
Solutions:
2.4 Inaccurate angle
Due to changes in material thickness, slight inconsistencies in the thickness of the metal plate will lead to angle deviation. Secondly, there is also the wear of the mold. Wear of the mold or punch during bending will produce uneven contact points. Finally, there is the reason for inaccurate setting of the machine bending parameters. Programming errors during machine operation and uncalibrated backgauges will affect the accuracy of the equipment.
Solution:
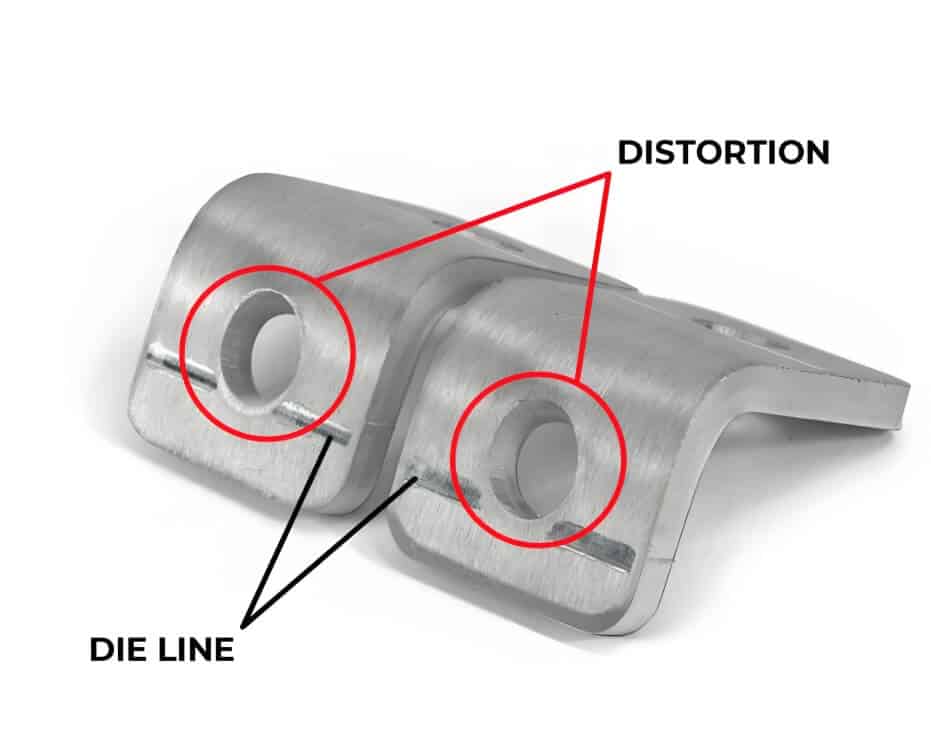
2.5 Scratches on the surface of the sheet
The following are the reasons for material scratches:
1. The surface of the raw material is rough, rusty or has other defects.
2. The clamping pressure of the fixture is too high.
3. The die pressure during the bending process is too high.
4. The bending radius of the upper die is too small.
5. The bending gap is too small, and the internal friction increases and causes damage.
Solutions:
2.6 Slippage and misalignment
During bending, material rebound will change the bending angle and cause the center line to shift. Or the workpiece is not placed accurately, the back gauge is not accurately positioned, and the clamping force of the fixture is insufficient, which may cause offset and misalignment.
Solution:
2.7 Cracks or fractures
Cracks and fractures are most likely to occur in brittle materials, such as stainless steel or aluminum, but may also occur in other materials.
First, when the material is subjected to excessive stress during the bending process, it will cause structural failure and fracture. In addition, too small a bending radius and too large a bending angle are also one of the reasons. Finally, the choice of die is also important. If the die opening is too narrow for the material thickness, it will increase the stress concentration on the bending line and cause cracks or fractures.
Solutions:
2.8 Uneven bending
Uneven bending may be caused by misalignment of the punch and die. Or uneven material thickness and hardness lead to deviation, or uneven die pressure distribution due to improper clamping.
Solution:
2.9 Overbending or underbending
Overbending or underbending occurs when the bending exceeds or fails to reach the required angle or exceeds the required angle. This is usually due to incorrect tool settings or inaccurate programming settings, and the elasticity of the material is not fully considered.
Solutions:
2.10 Bending causes hole deformation
The press brake performs elastic bending through hole positioning. Due to the friction between the lower die and the workpiece, the outer side of the bending arm is pulled, causing the positioning hole to deform.
Solution:
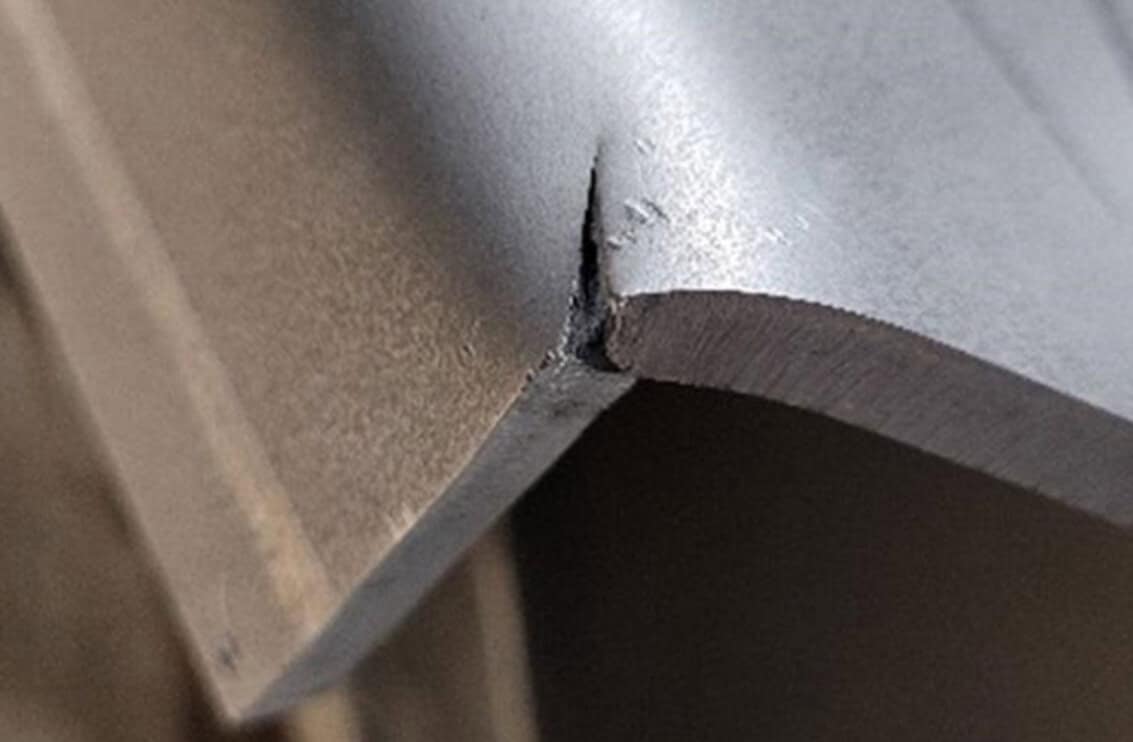
3. Measures to improve the bending accuracy of the brake press bending machine
3.1 Optimize material selection and pretreatment
First select smooth and defect-free materials to improve the surface of the bent product and the stability of the bending.
3.2 Select and maintain the right mold
Regularly check and polish the mold to reduce surface defects. If you encounter a worn mold, replace it in time to reduce friction and damage.
Note: For a detailed introduction to the press brake bending machine die, please refer to this article: Press brake tooling Complete Guide: Pictures and text both profuse, understood at one look!
3.3 Regularly calibrate the accuracy of the equipment
Regularly calibrate the important parts of the brake press, such as the machine tool guide rails. Back gauges, molds, etc., to ensure repeated positioning accuracy.
Note: For specific guidelines on the calibration and setup of bending machines, please read this article: Proper setup steps for Press brakes and analysis of common calibration issues
3.4 Reasonably set process parameters
Taking into account the rebound characteristics of the material, the CNC system can be used to adjust the parameters for bending compensation to correct errors caused by rebound, material thickness and other problems.
3.5 Operator training and safety regulations
Strengthen the technical training of front-line operators, standardize the operating procedures, strengthen safety awareness, and reduce the probability of human errors.
3.6 Increase lubrication and protection measures
The use of lubricants during the bending process can reduce material damage, and protective films can also be used to prevent surface damage.
4. Advanced and special bending issues
4.1 Bending challenges of special materials such as high-strength steel, aluminum alloys, and composite materials
It is difficult to control the bending results of high-strength materials, such as high-strength steel that is easy to rebound. Aluminum alloys are prone to cracking, so it is necessary to consider the material properties and stress distribution, and use special molds and parameters.
4.2 Common problems with complex shapes and multiple bends
Multiple bends can easily cause cumulative dimensional errors and positioning difficulties. It is necessary to accurately control the force and angle of each bend. Multi-axis synchronization technology and intelligent fixtures can be used to improve accuracy.
4.3 Unique bending difficulties for large or ultra-thin/ultra-thick plates
Long plates are prone to deformation and require multi-point support + step-by-step bending; ultra-thin plates (<1mm) are prone to wrinkling, and it is recommended to use elastic gaskets; ultra-thick plates (>10mm) require high tonnage + slow bending to prevent breakage.
4.4 New problems in intelligent/automatic bending (such as CNC synchronization error)
Automatic feeding and bending movements are not synchronized, which may cause positioning deviations. It is necessary to optimize the CNC program and install a laser correction system. Real-time pressure sensing can dynamically adjust parameters to reduce finished product errors.
5. Summary and Suggestions
The key to preventing press brake bending machine problems is to build a systematic management closed loop: from strict material testing, fine mold maintenance to intelligent equipment upgrades, supplemented by process standardization and employee skill improvement, to form a full-process quality defense line. At the same time, by continuously tracking process innovation, new material applications and automation technology development, companies can not only effectively avoid production risks, but also enhance product consistency and production line flexibility, thereby consolidating competitive advantages in a dynamic market.
Further Reading
Choose the Right Deflection Compensation System for Accurate Bending of Long Workpieces!
The Golden Rule: How to Operate a CNC Press Brake Correctly
Hydraulic Press Brake Troubleshooting: The Ultimate Guide to Fix Common Problems
Metal Laser Cutting Machine: Buyer’s Ultimate Guide to Costs, Types & Quality Factors
One Article to Master CNC Press Brakes: Types, Workflow, Structure & Buying Tips
What Is a Tandem Press Brake? Benefits, Applications & Buying Tips
The top 10 best press brake manufacturers in the world in 2025
How to Use a Press Brake Machine for Precise Bending: Essential Settings, Tools & Tuning
Definition, working principle and selection guide of hybrid press brake
Press Brake Bending Basics: Everything You Need to Know for Efficient Bending
CNC Laser Cutting Machines Comparison:CO₂ vs. Fiber vs. Diode
Ultimate Guide to Hydraulic Press Brake Maintenance: Top Tools, Schedules & Expert Tips
Post Your Review
Share Your Thoughts And Feelings With Others
Hello, Customers!
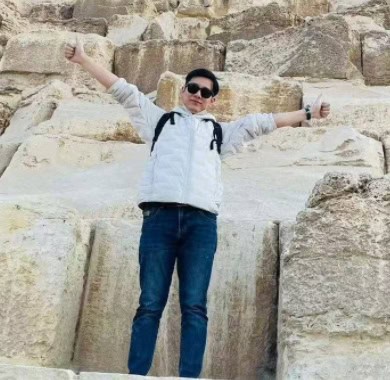
Author introduction
我叫Francis Pan,是RAYMAX的外贸经理。我从事金属制造和数控机械领域已有10多年。欢迎联系我们,我非常乐意为您提供最好的服务和产品。
邮箱: [email protected] | 微信: 13645551070
Top Guidelines
- Press Brake Air Bending: Guide to Principles, Calculations & Best Practices
- What Materials Can a Fiber Laser Cut? A Practical Handbook of Metals, Non-Metals & Limitations
- What is a Fiber Laser Cutting Machine? The Ultimate Guide for 2025
- What is Laser Cutting Machine? The Ultimate Guide for 2025
- Top 10 Fiber Laser Cutting Machine Manufacturers of 2025
- Press Brake Buyers Guide: Expert Tips to Select, Compare, and Buy with Confidence
- Hydraulic Press Brake Troubleshooting: The Ultimate Guide to Fix Common Problems
- Press Brake Radius Mastery: Inside/Outside Radius, 8× Rule, and Real-World Tips
- Press Brake Bending Basics: Everything You Need to Know for Efficient Bending
- Everything You Need to Know About Press Brake Fundamentals