This article mainly discusses the importance of press brakes in modern manufacturing, and mainly provides discussions on their basic functions, working principles of each classification, commonly used processing materials, and key factors in type selection. If you happen to be interested in these, or just happen to have the need to purchase press brakes, I hope the following article can answer your questions, or you can also contact our experts for consultation.
The Importance of Press Brakes in Modern Manufacturing
Press brakes are crucial processing equipment in modern manufacturing. They control the bending angle, radius, and size of sheet metal materials with high precision, high speed, and batch production to help manufacturers manufacture complex sheet metal bending components with consistent precision and ensure the consistent quality of each product component. In addition, professional press brake equipment can also help manufacturers improve profitability and production competitiveness by optimizing production workflows, while reducing material waste, increasing employee work speed, and protecting the safety of sheet metal materials and workers.
Features:
1. Automated and efficient production
Press brakes use automated precision control and batch production to achieve high-quality and consistent bending results. Greatly improve the quality of finished products and production efficiency of sheet metal manufacturing.
2. Flexibly respond to changing market demands
Modern press brakes are used in multiple metal processing fields. According to the diversified needs of different industries, various customized production of sheet metal materials can be realized.
3. Ensure the consistency of parts
Through the precise calculation and control of the CNC system, the CNC press brake can ensure the high consistency of each batch of sheet metal parts after processing.
Basic functions and uses of press brakes
Control the bending angle, radius and size of metal sheets, and accurately bend metal sheets into various structural shapes required by manufacturers. The main functions are sheet metal bending, multi-dimensional (multi-station, multi-step) complex bending, and batch automation processing through programming.
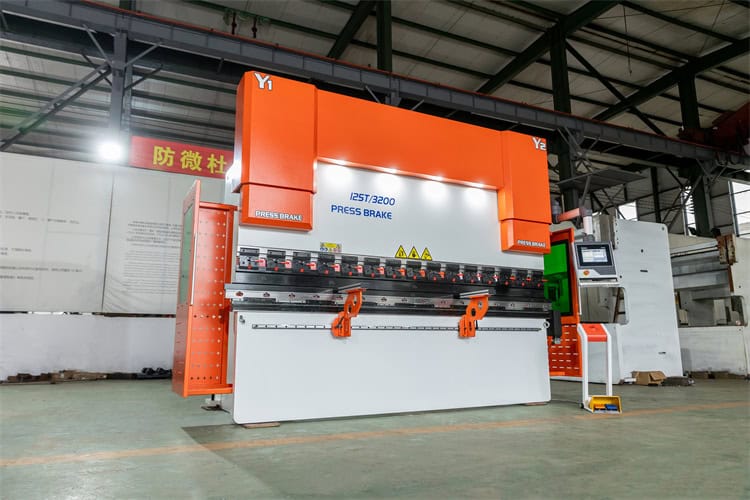
Working principle of press brake
1. Working principle of hydraulic press brake
The hydraulic cylinder pushes the slider up and down, the servo valve realizes high-precision position control, and the hydraulic system continuously and stably outputs large tonnage to realize the bending of metal plates.
2. Working principle of mechanical press brake
Using the power of the mechanical flywheel, the motor drives the crank-connecting rod mechanism, and the mechanical power transmission system realizes the action of pressing the plate down. This press brake is suitable for light bending processing. It has a simple structure but low precision. It has been gradually replaced by other press brakes in the market.
3. Working principle of electric press brake
The servo motor is used to directly drive the screw to achieve precise plate bending. Because there is no hydraulic oil pollution, it is simple to maintain, quiet and noiseless, and suitable for modern green production requirements.
4. Brief description of the advantages and disadvantages of each system
Main applications of press brakes
The application fields of press brakes are quite broad, including the automotive industry, aerospace, construction industry, metal furniture, home appliance industry, electrical industry, engineering machinery, shipbuilding, rail transportation, pharmaceutical and food processing, decorative materials, energy industry, stainless steel products, decoration industry, power equipment, steel structure manufacturing, electromechanical engineering, heavy machinery industry, etc.
Common processing materials and part types of press brakes
1. Commonly used metals in the brake forming process include: stainless steel, carbon steel, aluminum plate, high-strength alloy, brass and copper, etc. Among them, Raymax’s press brake can process any metal sheet with a bending length of 20-100 tons and 900 to 3100 mm.
2. Common part types: brackets, housings, junction boxes, sheet metal cabinets, vehicle parts, tool boxes, decorative parts, etc.;
Key factors for selecting press brakes
1. Load capacity (tonnage)
Calculate the required bending tonnage based on the thickness and bending length of the sheet metal material. A large-tonnage press brake is required for thick plate processing; while a small-tonnage press brake such as an electric press brake is suitable for the processing of fine workpieces.
2. Length
Match the press brake according to the length of the workpiece. The length of the press brake must be sufficient to cover the bending length of the largest sheet.
3. Precision
High-precision bending products require press brakes with more axes to process, such as 6-axis press brakes, 8-axis press brakes, etc.
4. Material type
Different metal materials (such as aluminum vs. stainless steel) have different requirements for bending radius, pressure, and mold adjustment.
How to choose the right model according to your needs (applicable scenario analysis)
According to the processing type, you can quickly determine the model that suits you:
Maintenance and safe operation of press brakes
1. Common maintenance tips
Regularly check the hydraulic oil status, lubricate the guide rails, etc.;
2. Safety operation guide
Correctly wear protective equipment, and it is strictly forbidden to touch the mold when the machine is running. You can also purchase relevant protective devices, such as the LazerSafe laser protection system, to protect your operator in all directions.
3. Industry standards and certifications
Press brakes on the market that meet international safety standards such as EU CE and ISO can be purchased by yourself.
Conclusion
The above is the overview of press brakes summarized by Raymax for you today. If you happen to have the need to buy a press brake, don’t know how to choose a model, or have other technical questions about press brakes, you can directly contact our staff. We will serve you free of charge 7*24 hours. For more knowledge about press brakes, please stay tuned!
Further Reading
How to Choose a Press Brake Control System? Function, Brand & Buying Guide (Including Delem/ESA)
What is Laser Cutting Machine? The Ultimate Guide for 2025
Press Brake Tonnage Explained: Learn How to Calculate for Optimal Performance
What is a Press Brake Operator? Duties, Skills, Salary & Career Prospects Explained!
Ultimate Guide to Hydraulic Press Brake Maintenance: Top Tools, Schedules & Expert Tips
Press Brake Dies Explained: Types, Applications, and golden rule of selection
Press brake tooling Complete Guide: Pictures and text both profuse, understood at one look!
CNC Press Brake Axis: Mastering Configurations from 2-Axis to 8+1 for Pro Results
What Is a Tandem Press Brake? Benefits, Applications & Buying Tips
Definition of press brake tool material
The Complete Guide to Press Brake Techniques:11 Types of sheet metal pressing process Explained
Press Brake Radius Mastery: Inside/Outside Radius, 8× Rule, and Real-World Tips
Post Your Review
Share Your Thoughts And Feelings With Others
Hello, Customers!
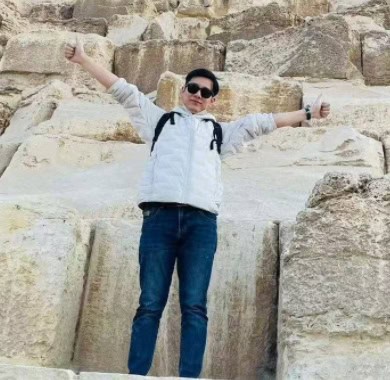
Author introduction
我叫Francis Pan,是RAYMAX的外贸经理。我从事金属制造和数控机械领域已有10多年。欢迎联系我们,我非常乐意为您提供最好的服务和产品。
邮箱: [email protected] | 微信: 13645551070
Top Guidelines
- Press Brake Air Bending: Guide to Principles, Calculations & Best Practices
- What Materials Can a Fiber Laser Cut? A Practical Handbook of Metals, Non-Metals & Limitations
- What is a Fiber Laser Cutting Machine? The Ultimate Guide for 2025
- What is Laser Cutting Machine? The Ultimate Guide for 2025
- Top 10 Fiber Laser Cutting Machine Manufacturers of 2025
- Press Brake Buyers Guide: Expert Tips to Select, Compare, and Buy with Confidence
- Hydraulic Press Brake Troubleshooting: The Ultimate Guide to Fix Common Problems
- Press Brake Radius Mastery: Inside/Outside Radius, 8× Rule, and Real-World Tips
- Press Brake Bending Basics: Everything You Need to Know for Efficient Bending
- Everything You Need to Know About Press Brake Fundamentals