1. Introduction
Hydraulic press brake machine as metal bending equipment, regular maintenance is critical. Reasonable maintenance can extend the life of the equipment, not only to reduce the occurrence of equipment failure, but also to reduce the sudden failure and downtime, which helps to improve productivity and reduce maintenance costs.
Below we will introduce in detail the tools and equipment needed for hydraulic press brake maintenance, regular inspection and maintenance rules, special maintenance parts of the scientific maintenance methods, common troubleshooting ideas, as well as related notes.
2. what tools and equipment are needed for the hydraulic press brake maintenance ?
2.1 Protection tools
2.2 Cleaning Tools
2.3 Measurement and Inspection
The main purpose of measuring instruments is to calibrate components.
2.4 Alignment and Repair
2.5 Electrical Maintenance
2.6 Other essential tools and equipment
2.7 Safety equipment
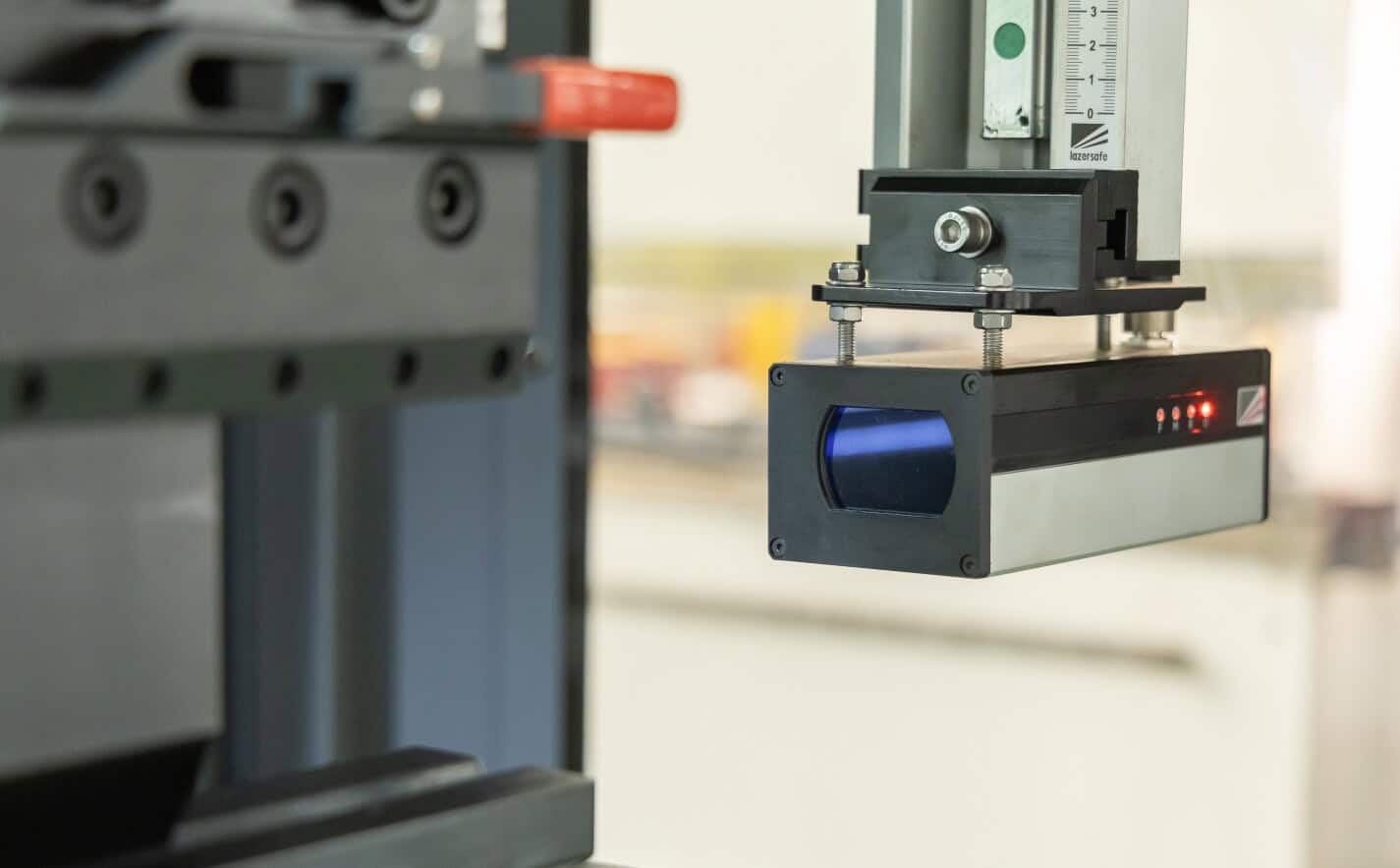
3. Hydraulic press brake regular inspection and maintenance tasks
3.1 Daily tasks
① Clean the equipment and working area before and after work.
② Check the hydraulic oil level and check for leakage.
③ Lubricate the moving parts according to the lubrication chart.
④ Check the oil level in the tank, and prohibit the operation if the oil level is lower than the lower limit.
⑤ Check the electrical components for any loose connection or damage.
⑥ Check the molds for any defects and cracks, and check the alignment.
⑦ Test the bending to calibrate the back gauges.
⑧ Check the conditions of the punches and the molds, and alignment.
⑨ Check protection and safety devices such as emergency stop buttons, rear and side guards, and air filters for timely replacement.
3.2 Monthly Tasks
① Lubricate the equipment according to the equipment manual, such as bearings, sliders, swing arms and other moving parts, wipe off excess grease after lubrication.
② Check the hydraulic oil level and replenish it in time.
③ Clean the hydraulic circuit and external parts. Including valves, pumps, motors and other small parts.
④ Check the hydraulic system for leaks. Check the oil circuit assembly, joints, seals for oil seepage, oil mist, oil beads hanging on the wall. If looseness is found, turn off the main power and tighten with tools. If the seals are found to be aging and cracked, replace the seals with the same specification.
⑤ Check the hydraulic oil tank air filter is not blocked moisture oil, and timely cleaning or replacement.
⑥ Clean the electrical cabinet and control panel filters.
⑦ Check all bolted connections, and use a torque wrench to double-check each item according to the instructions.
3.3 Quarterly tasks
① Check the sealing status of the hydraulic system and the cylinder for wear and tear.
② Check for oil leakage.
③ Clean or replace hydraulic oil filter
④ Check electrical components for signs of looseness or overheating.
⑤ Calibrate the control system and limit elements, debug the back gauge shaft limit, machine travel, switches.
⑥ Check that safety devices, safety light curtains, emergency stop buttons, foot switches, and other devices are functioning properly.
⑦ Check that punches and molds are aligned.
3.4 Annual tasks
① Replace the hydraulic oil and filter, main oil filter and return oil filter element replacement, if necessary, drain the tank sediment and then clean the inside of the tank.
② Check and calibrate hydraulic press brake circuit protection devices.
③ Check and maintain the hydraulic system.
④ Check and maintain the hydraulic press brake guide rails, retaining fingers, back gauges, shafts, and ball screws.
⑤ Check and maintain all hydraulic press brake mechanical parts.
⑥ Check and maintain all hydraulic press brake tools.
⑦ Check and update the hydraulic press brake control system software.
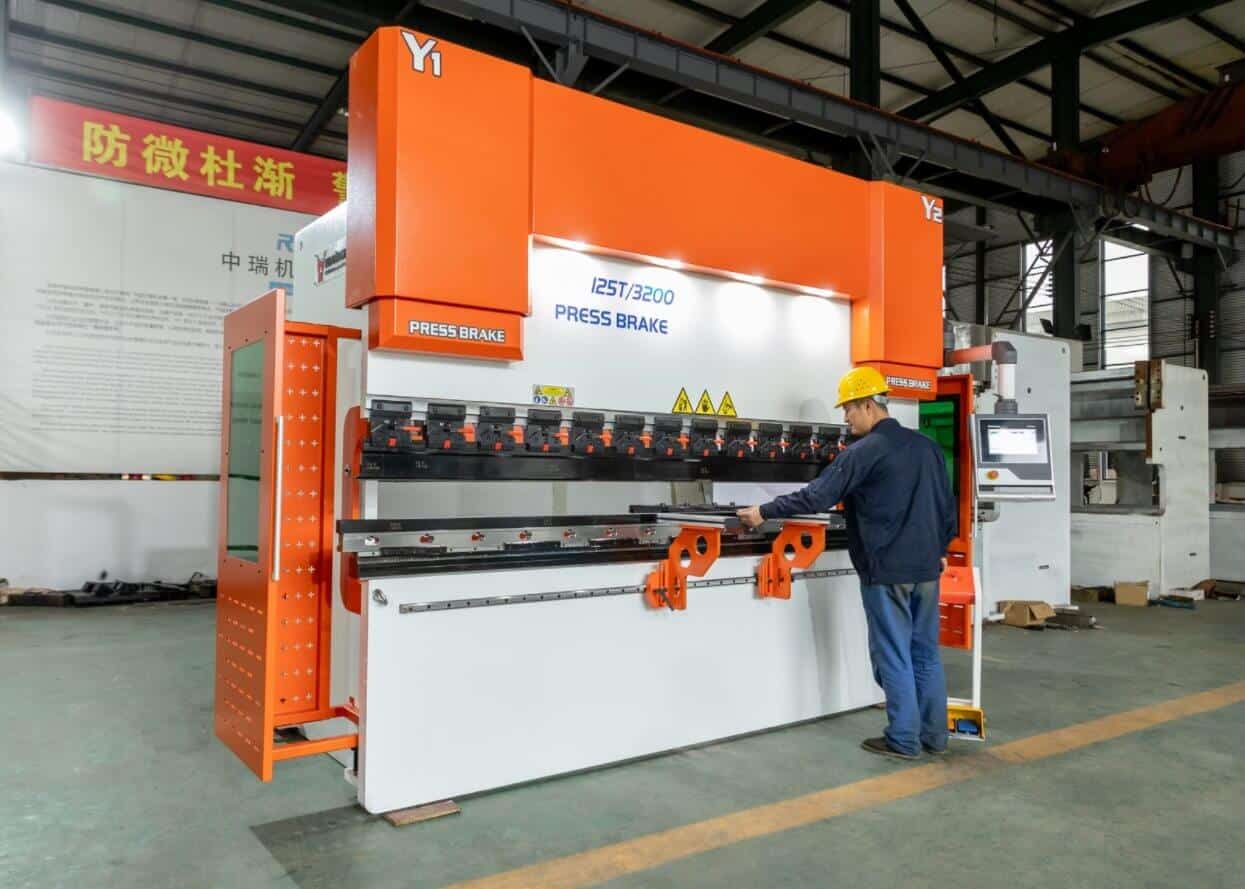
4. hydraulic press brake special maintenance parts
4.1 Hydraulic circuit
Hydraulic circuit consists of tanks, valve manifolds, pipelines, motors, pumps, etc..
4.2 Mechanical parts
4.3 Lubrication System
① It is recommended to lubricate and clean all moving parts on the hydraulic press brake. This includes ball screws, guide rails, back gauges, gears, etc. These parts should be lubricated at least once a week and some parts may even require daily lubrication.
② Clean the parts before lubrication and use the specified oil, no mixing is allowed.
③ Do not over lubricate or it will lead to insufficient friction or contamination of parts.
4.4 Electrical equipment
4.5 Tooling system
4.6 Back gauge and positioning system maintenance
4.7 Safety and protection maintenance of hydraulic press brake
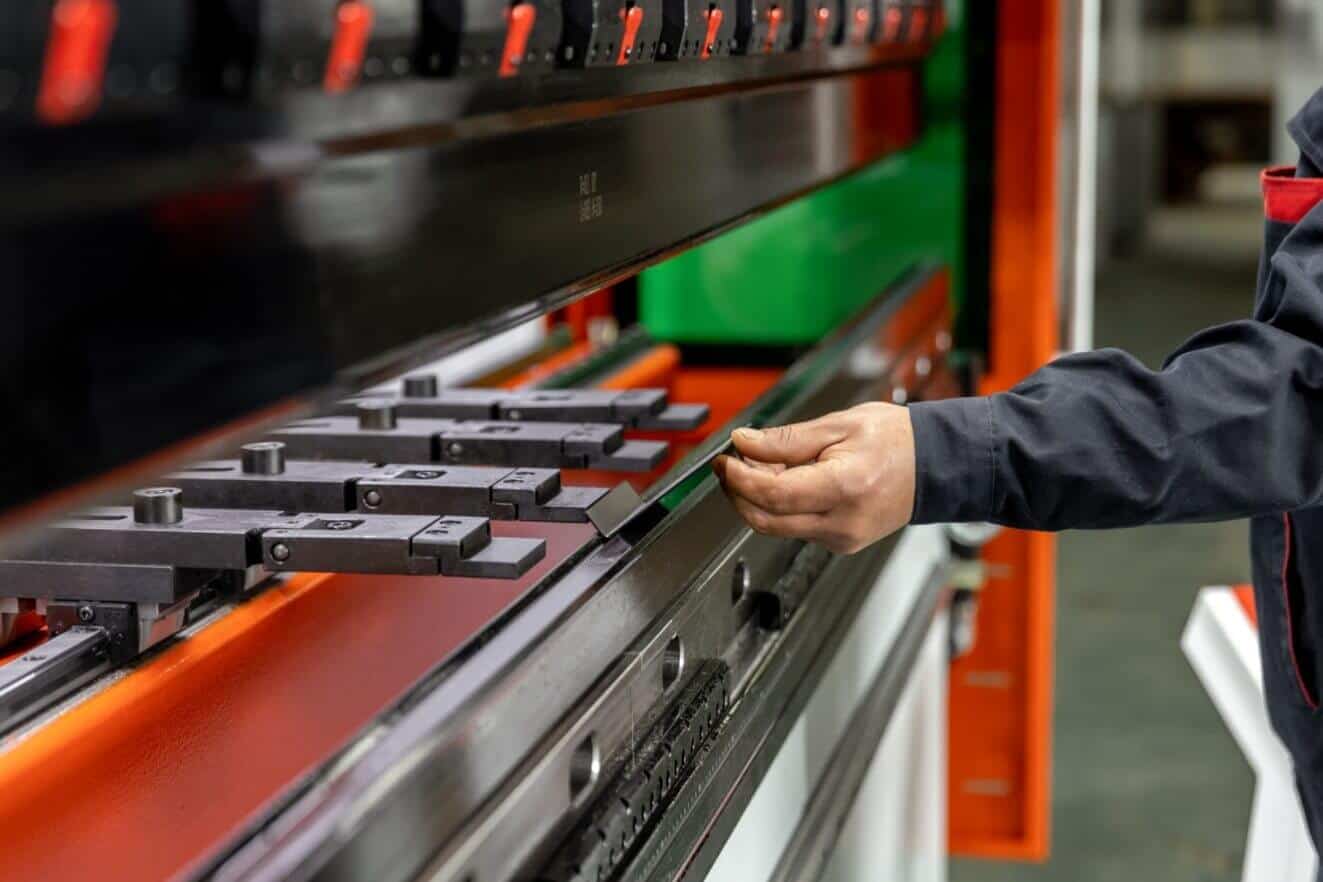
5. Common Failures and Troubleshooting
5.1 Hydraulic system pressure is insufficient how to troubleshoot
Check whether the oil level is low, hydraulic fluid deterioration, if the timely replacement of fluid.
Check the status of hydraulic pumps and motors to see whether the overheating led to failure.
Check all the valves, tubes and seals for leaks, if any need to be tightened or replaced
5.2 Circuit failure how to quickly locate
Observe the electrical cabinet alarm indicator, double-check each circuit fuse, relay, contactor is blown.
Check whether the power supply is normal, use a multimeter to test whether the wires and electrical connections are damaged or loose.
Check the cnc program error message, check the abnormality against the manual.
5.3 The cause analysis of abnormal noise and vibration
Check whether the mechanical parts have loose bolts and poor lubrication.
Check whether the suction pipe is leaking, the oil pump is worn out, and the oil has air bubbles which can also cause abnormal noise.
Check whether the mold is installed in place.
5.4 Mold wear leads to bending error troubleshooting
Regularly check the degree of wear of the mold and replace it in a timely manner.
Check the tightness of the bolts between the mold and the table and slider.
Check whether the mold size error.
5.5 press brake lubrication cycle
The lubrication frequency of the press brake is differentiated by components, such as the back gauge, guide rail, ball screw should be lubricated once a week, while other components such as the guide rail of the moving beam only need to be lubricated once a year. Note: high dust, high load conditions, then shorten the interval.
5.6 What is the preventive of the hydraulic press brake maintenance?
Regularly change the hydraulic oil and oil filter. Drain the old oil, clean the oil tank and install a new oil filter.
Regularly lubricate the moving parts of the hydraulic press brake.
Regularly test safety guards and electrical components.
Make backup copies of production data and CNC programs to prevent misuse and accidental loss.
5.7 What are the OSHA requirements for press brakes?
OSHA standards require that effective machine guarding and safety interlocks must be provided, and that all operators and tools must be kept out of the mold closure area.
Requirements for regular maintenance, ledger records, and tagged maintenance systems; emergency stops, interlocks, light curtains, etc. must be shut down immediately for maintenance in the event of a failure.
Employees are required to undergo formal safety training and are not allowed to operate the press brake with items/accessories that are not related to the main control.
6. Summary
Regular hydraulic press brake maintenance is a very important part. Proper installation and maintenance of the press brake can extend the life of the press brake and can minimize the occurrence of malfunctions.
The following provides a maintenance schedule template and tool list that the operator can refer to for maintenance tasks.
Maintenance intervals 10916_586aa6-36> |
Contents (examples) 10916_7b0777-fb> |
Responsible person 10916_5eb63f-b7> |
Daily 10916_c4aa82-b0> |
Cleaning, oil level, lubrication 10916_70cb41-63> | 10916_266ca4-70> |
Weekly 10916_0fa3ae-20> |
Key parts protection check 10916_5ff366-f4> |
Press brake operator 10916_977253-42> |
Monthly 10916_ec2655-e5> |
Bolt tightening, tank air filtration 10916_5295b0-cd> |
Equipment manager 10916_b12cf7-53> |
Quarterly 10916_3e6432-9c> |
Oil quality test/safety device calibration 10916_df7d6b-d1> |
Dedicated service technician 10916_432d13-dc> |
Yearly 10916_641a5b-51> |
Yearly Full fluid change, system overhaul 10916_da04a7-de> |
Mechanic/manufacturer’s engineer 10916_6e07c7-8c> |
6.1 Recommended maintenance tool list
Lubrication gun, grease, special cleaner, bolt tightening tool, pressure gauge, rag.
Multimeter, terminal crimper, CNC backup disk, several seals, self-priming pump, first aid kit, etc.
6.2 Precautions
All operations must be disconnected before power, hydraulic pressure relief, with special supervision.
All maintenance should be recorded and regularly filed for inspection.
Use regular hydraulic press brake manufacturer’s accessories and oil to prevent damage to equipment or safety accidents.
Further Reading
Ultimate Guide to Press Brake Punches: Eleven Types, Materials, Selection, and Maintenance
CO2 vs Fiber Laser Cutting Machine: Which Machine Should You Use? (Raymax Guide)
Proper setup steps for Press brakes and analysis of common calibration issues
The top 10 best press brake manufacturers in the world in 2025
Press Brake Software: Basics, Implementation, Examples & Selection Guide
How to Choose a Press Brake Control System? Function, Brand & Buying Guide (Including Delem/ESA)
10 Press Brake Bending Problems and How to Fix Them in Sheet Metal
CNC Press Brake Axis: Mastering Configurations from 2-Axis to 8+1 for Pro Results
One Article to Master CNC Press Brakes: Types, Workflow, Structure & Buying Tips
Metal Laser Cutting Machine: Buyer’s Ultimate Guide to Costs, Types & Quality Factors
What Materials Can a Fiber Laser Cut? A Practical Handbook of Metals, Non-Metals & Limitations
Choose the Right Deflection Compensation System for Accurate Bending of Long Workpieces!
Post Your Review
Share Your Thoughts And Feelings With Others
Hello, Customers!
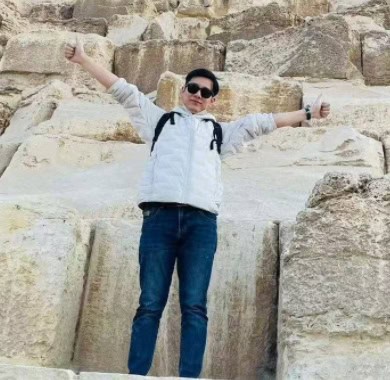
Author introduction
我叫Francis Pan,是RAYMAX的外贸经理。我从事金属制造和数控机械领域已有10多年。欢迎联系我们,我非常乐意为您提供最好的服务和产品。
邮箱: [email protected] | 微信: 13645551070
Top Guidelines
- Press Brake Air Bending: Guide to Principles, Calculations & Best Practices
- What Materials Can a Fiber Laser Cut? A Practical Handbook of Metals, Non-Metals & Limitations
- What is a Fiber Laser Cutting Machine? The Ultimate Guide for 2025
- What is Laser Cutting Machine? The Ultimate Guide for 2025
- Top 10 Fiber Laser Cutting Machine Manufacturers of 2025
- Press Brake Buyers Guide: Expert Tips to Select, Compare, and Buy with Confidence
- Hydraulic Press Brake Troubleshooting: The Ultimate Guide to Fix Common Problems
- Press Brake Radius Mastery: Inside/Outside Radius, 8× Rule, and Real-World Tips
- Press Brake Bending Basics: Everything You Need to Know for Efficient Bending
- Everything You Need to Know About Press Brake Fundamentals