1. Introduction
Looking back at history, the early press brake punches had a simple structure and could only perform basic stamping operations, but with the development of industry, modern press brake punches were gradually born. Today, punches play a vital role in the field of precision manufacturing with micron-level precision. From the initial prototype to the core object of today’s manufacturing industry, punches have witnessed and promoted the vigorous development of the manufacturing industry. Through this article, you can learn some basic knowledge about press brake punches, including what press brake punches are, the main classification of punches, what materials punches are made of, and how to choose a suitable press brake punch and the daily maintenance of punches, so that you can fully understand this very important accessory for bending.
2. What is a press brake punch?
2.1 Definition of a punch and its function in a press brake
2.1.1 Definition: Upper and lower dies of a brake press, punch: the top die of a brake press, that is, the upper die. Apply force to the metal to be bent, and bend the sheet together with the lower die.
2.1.2 Function: Apply necessary force to the metal to be processed, responsible for bending the material into a predetermined shape.
2.2 The difference and cooperation between punch and die
2.2.1 Difference: Punches generally apply bending force to the workpiece. Press brake dies are used to fix the workpiece, support and limit the forming.
2.2.2 Cooperation: The two complement each other, one applies force and the other supports, and together complete the entire bending process.
3. Main types of punches for press brakes
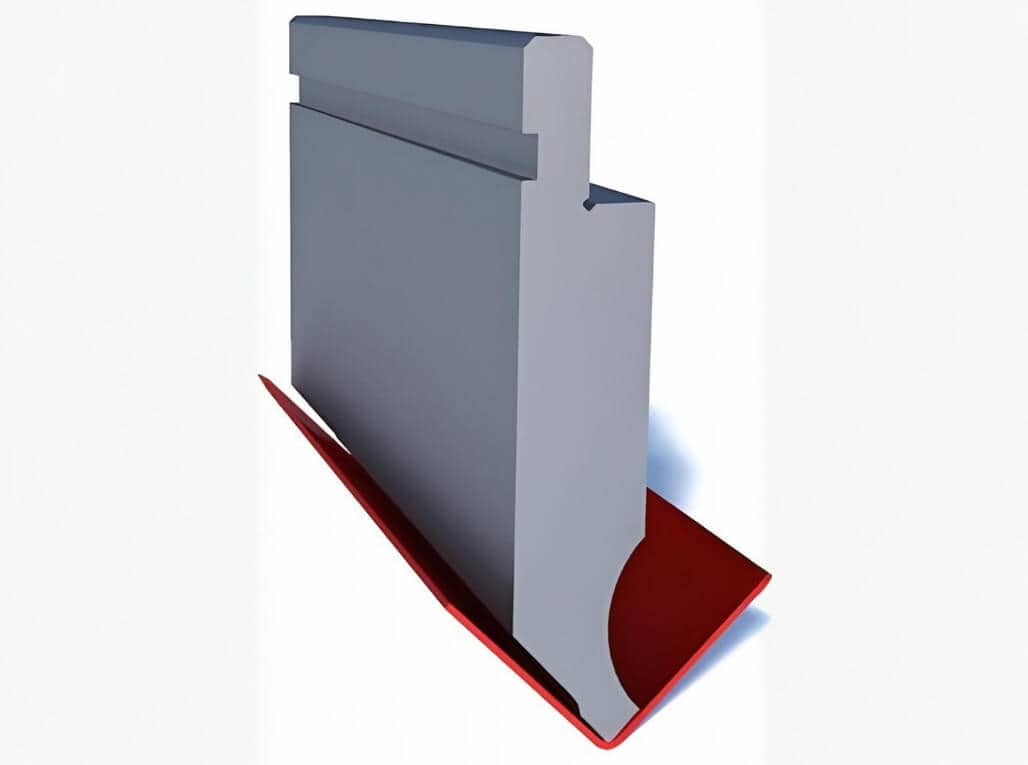
3.1 Standard punching
A relatively thick body and a very thin punch, the best effect for processing thicker plates or larger pieces. It has a feature that the inner and outer sides are slightly concave and relatively flat, and can be made into a relatively short flange fold. Why is it called standard? It is because this is more common and can be used in most cases.
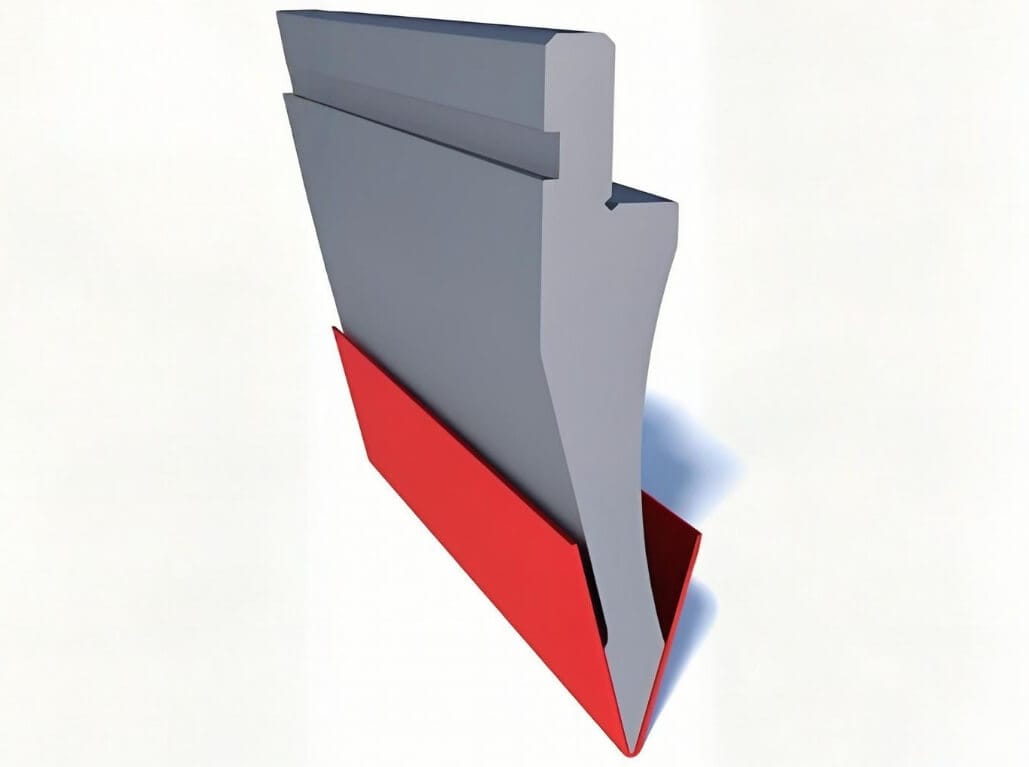
3.2 Acute Angle punch
This shape is very sharp and the bending angle is also small (30~60 degrees). It is very suitable for products that require a small bending angle, because the bending range is small and the quality of the finished product will be better.
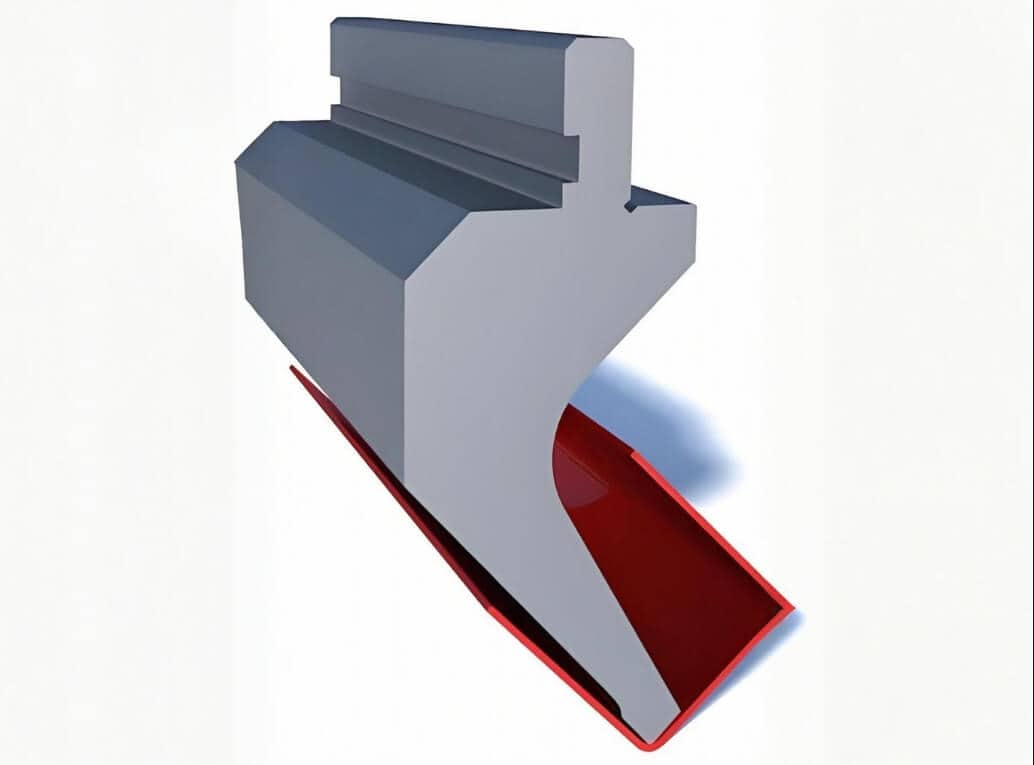
3.3 Swan neck (Goose neck punch)
There is a very strange “goose neck”. This punch is “U” shaped. The “U” shape makes the U-shaped profile easier to form because it prevents the bent legs from colliding with the mold frame when bending. It is generally used for products with deeper frames or high flanges.
3.4 Curved punch
A curved shape, a curved bending design for metal sheets, which can be used in combination with some other standard punches or gooseneck punches.
3.5 Belt punch
Thin and small, used to punch holes in belts/belts.
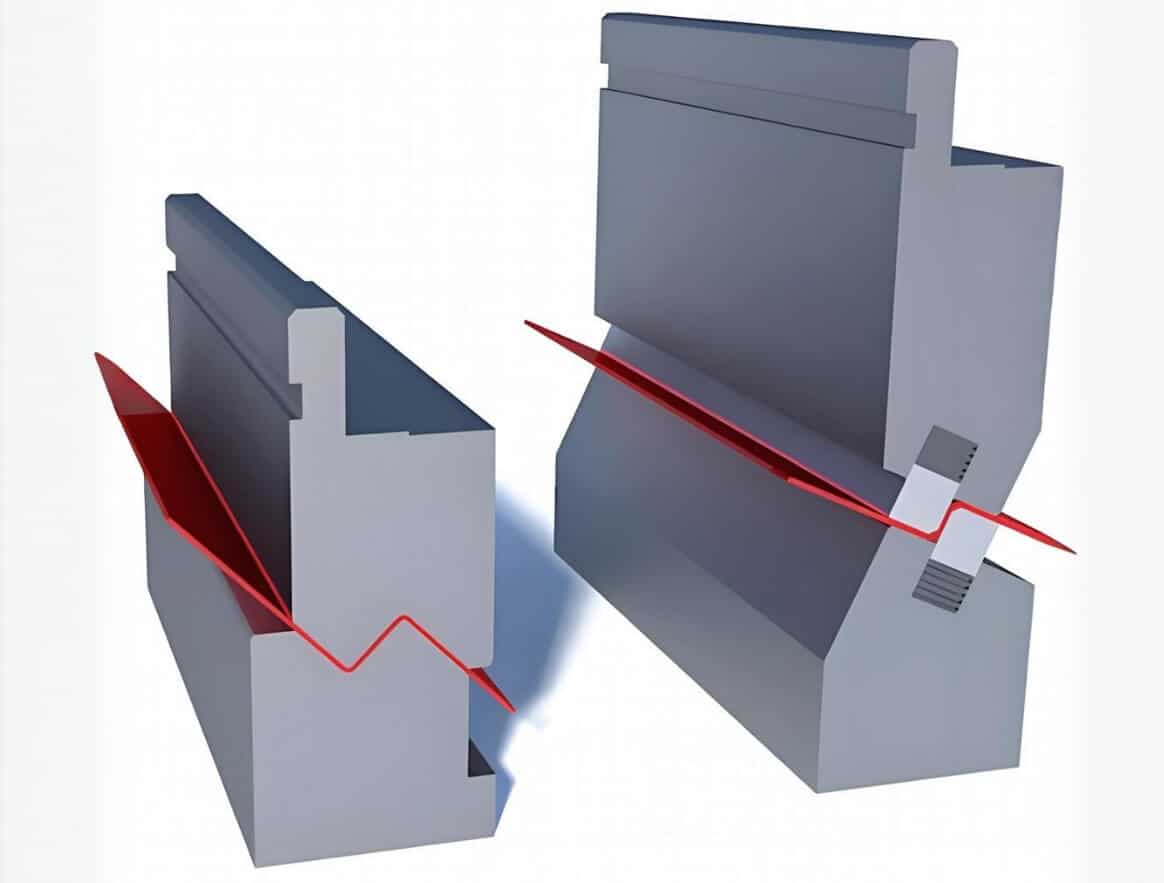
3.6 Engagement punch (Z type)
Z-shaped tools can be used at the corners of the material. The shape characteristics can make the material form an S shape, which is the most ideal tool.
3.7 Straight punch
It can complete small angle and small size bending; it can bend 90 degrees on materials such as low carbon steel, stainless steel and aluminum, and is also the best measurement tool for testing material tensile and ductility.
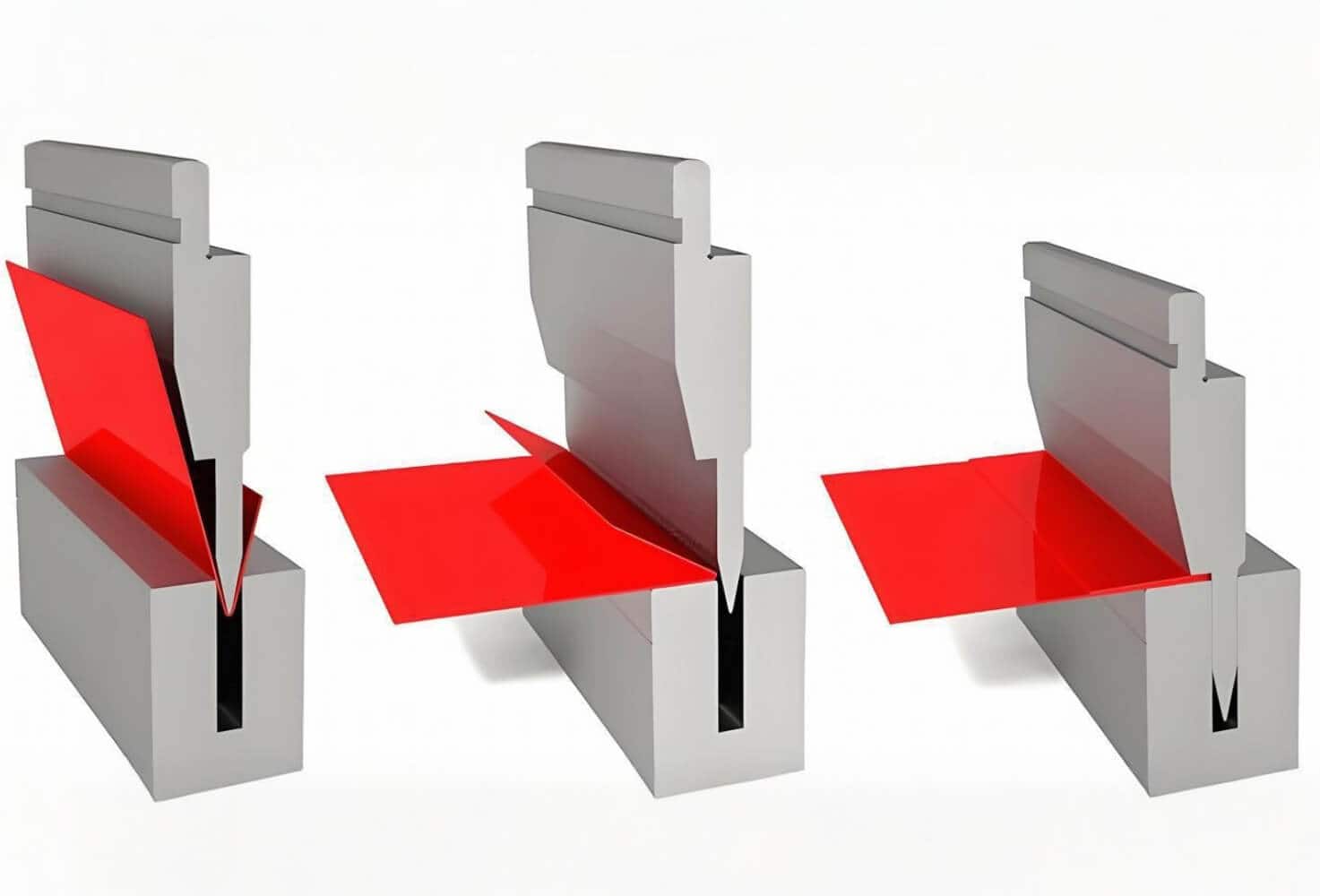
3.8 Curling punch
Used for curling the edge of metal plates to enhance the structural strength of metal edges.
3.9 Radius punch
Control the radius size to achieve different curvature effects and realize different arc processing.
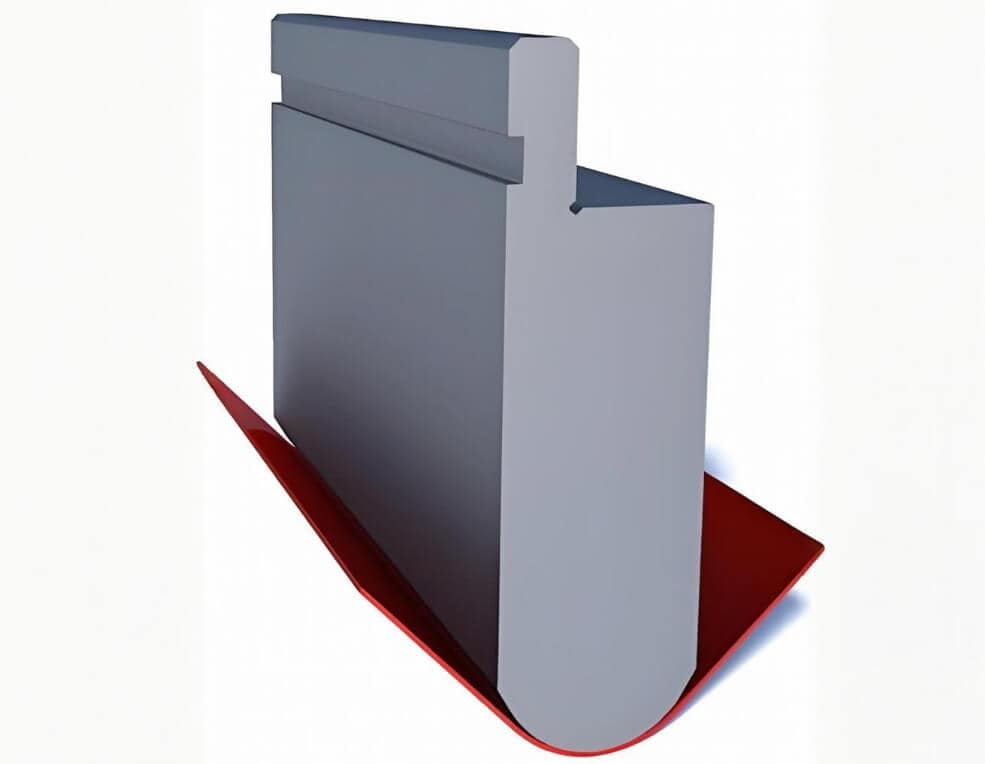
3.10 U-shaped punch
U-shaped punch, used to form a U-shaped groove.
3.11 Multi-V-shaped punch
Punch for processing complex parts, multiple V-shaped punches are used in rotation to reduce mold replacement.
4. Common materials and manufacturing processes of punches
4.1 Common materials (such as 42CrMo, Cr12MoV, high-speed steel, etc.)
The materials used to make punches are required to have high hardness, high toughness and wear resistance. For example, there are high-strength 42CrMo,
high-load Cr12MoV and high-speed precision high-speed steel.
Related technical reading : Definition of press brake tool material
4.2 Heat treatment and surface treatment methods (such as quenching, nitriding, etc.)
General punches need to be quenched to be so hard. If you want to achieve perfection, high-end products will use laser surface quenching, nitriding or welding to improve the service life and durability of the punch.
4.3 Manufacturing accuracy and its impact on the final bending quality
More accurate punches can bend workpieces with higher requirements with an error of about 0.1mm, with better bending effect and longer service life.
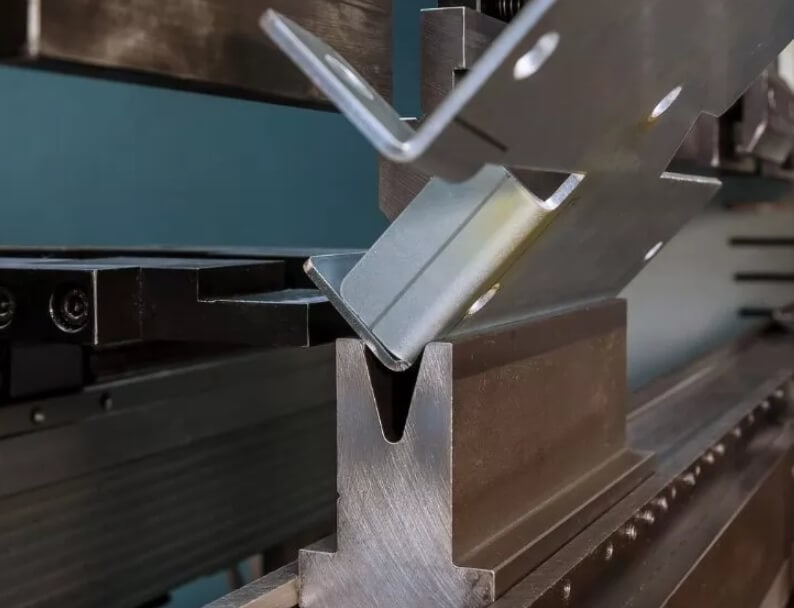
5. How to choose a suitable press brake punch
5.1 Material thickness
The thickness of the material determines what kind of punch to use. For example, if the material is thicker, a standard punch with large tonnage and high pressure must be used for processing, and vice versa. If it is relatively thin, it is necessary to choose a gooseneck punch or an acute-angle punch with different degrees of sophistication according to the different accuracy requirements.
5.2 Bending angle and bending radius
The bending angle and bending radius should also use different types of punches according to different needs, for example: choose a sharp angle punch for an acute angle of 30° to 60°, and choose an arc punch for a circular arc.
5.3 Compatibility with the mold
The size and shape of the upper and lower molds of the punch are consistent, which can increase synergy.
5.4 Precision and efficiency
If it is a workpiece that requires precision, the speed cannot be too slow; or if the quantity is large, consider production efficiency.
5.5 Consider wear resistance, life and maintenance cost
The press brake punch is affected by factors such as production scale and production use time. Standard punches are more durable, and other high-precision punches have a very short lifespan.
5.6 The trade-off between standard parts and customized parts
Standard punches are preferred for common processes, and customized punches are recommended for special bending scenarios.
6. Daily maintenance and care of press brake punches
6.1 Correct installation and calibration
The brake press punch is installed in a fixed slot, and the installer shall calibrate the production accuracy before commissioning.
Related technical reading : Proper setup steps for Press brakes and analysis of common calibration issues
6.2 Inspection and use process
The inspector should pay attention to observe whether the punch surface is worn, cracked, and deformed.
6.3 Cleaning, rust prevention and storage methods
After each use, the dirt should be washed away with a detergent, otherwise it is easy to get stuck and damage the punch. Anti-rust oil should be applied after use. The mold should not be exposed to moisture or chemicals, and it should be safely fixed in a metal cabinet using foam or plastic.
6.4 Recommendations on loss and replacement cycle
Determine the replacement cycle according to the actual wear and failure situation. It is recommended to replace it every shift when it is used frequently.
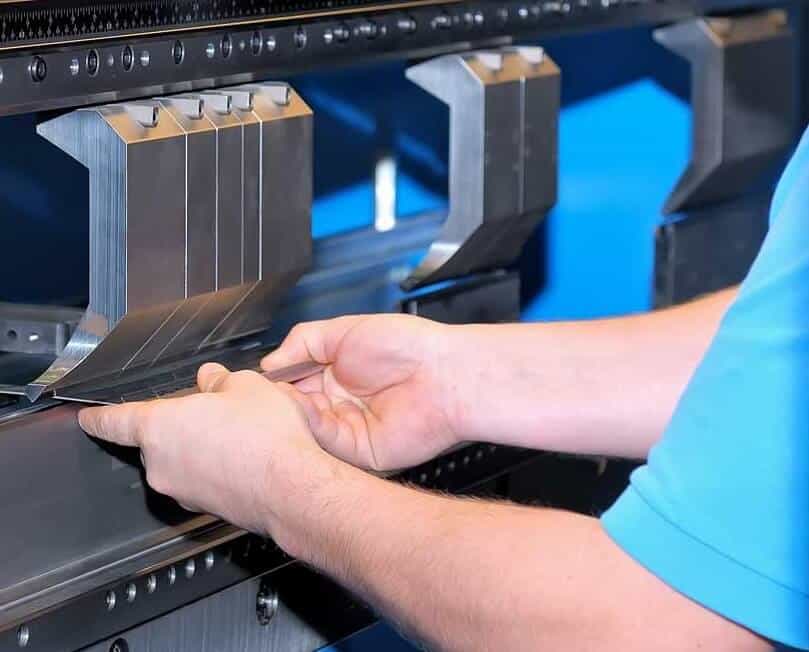
7. Factors affecting the performance of the brake press punch
7.1 Material thickness
In terms of material thickness, thicker materials require large bearing capacity molds, high hardness and toughness; on the contrary, thinner materials must first reach a certain precision before they can be processed and used.
7.2 Bending angle
Material angle bending is an important way to keep the deformation. Most special angles require special molds to be bent, which will not only avoid product defects, but also increase the life of the mold.
7.3 Texture direction
The texture position between different materials affects the product to a great extent. The direction along the grain will directly cause the product to crack and form defective products; while the direction against the grain increases the consumption of material energy and increases the unavoidable consumption.
7.4 Rebound effect
The effect of rebound directly determines the final bending degree and angle. Before forming, it is necessary to consider the different materials accordingly, and choose different sizes according to the punch model for production.
8. Conclusion
A good and efficient press brake punch can increase the output of the product and ensure the quality of the product. A good punch can reflect the level of a manufacturer. As the saying goes, “Excellent products attract customers.” Good punches can produce high-precision industrial products, and establishing high-quality products can produce a strong brand effect and impact, attract many customers, and gain a place in the same industry.
Here, RAYMAX suggests that if you are looking for a suitable bending press for your project, first directly contact your machine equipment supplier. Generally, they will professionally provide the corresponding type of press. You can also look for world-renowned press brake tool manufacturers. This type of press product can usually fully cover your project requirements and has complete after-sales guarantees!
Of course, as a professional press brake manufacturer , RAYMAX also has a series of professional and complete press brake mold supporting equipment. If you don’t want to worry anymore, you can also directly consult us. No matter who you purchase from or not, we will provide 7* 24-hour free technical services online! As a leading enterprise in the press brake manufacturing industry, RAYMAX hopes to provide the most effective assistance to all users in the field of CNC mechanical metal manufacturing! Welcome to contact us ~
Further Reading
The Ultimate Guide to Press Brake Metal Thickness
Press Brake Bending Basics: Everything You Need to Know for Efficient Bending
What Is a Tandem Press Brake? Benefits, Applications & Buying Tips
Top 10 Fiber Laser Cutting Machine Manufacturers of 2025
What is a Fiber Laser Cutting Machine? The Ultimate Guide for 2025
The top 10 best press brake manufacturers in the world in 2025
Everything You Need to Know About Press Brake Fundamentals
The Ultimate Guide to Press Brake Safety Devices and Guidelines for 2025
The Ultimate Guide to Fiber Laser Cutting Machine Working Principles, Components, Workflow and Process Parameters
Definition, working principle and selection guide of hybrid press brake
One Article to Master CNC Press Brakes: Types, Workflow, Structure & Buying Tips
Metal Laser Cutting Machine: Buyer’s Ultimate Guide to Costs, Types & Quality Factors
Post Your Review
Share Your Thoughts And Feelings With Others
Hello, Customers!
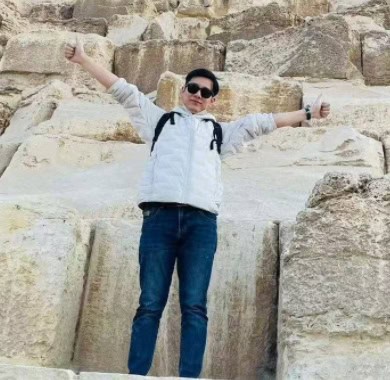
Author introduction
我叫Francis Pan,是RAYMAX的外贸经理。我从事金属制造和数控机械领域已有10多年。欢迎联系我们,我非常乐意为您提供最好的服务和产品。
邮箱: [email protected] | 微信: 13645551070
Top Guidelines
- Press Brake Air Bending: Guide to Principles, Calculations & Best Practices
- What Materials Can a Fiber Laser Cut? A Practical Handbook of Metals, Non-Metals & Limitations
- What is a Fiber Laser Cutting Machine? The Ultimate Guide for 2025
- What is Laser Cutting Machine? The Ultimate Guide for 2025
- Top 10 Fiber Laser Cutting Machine Manufacturers of 2025
- Press Brake Buyers Guide: Expert Tips to Select, Compare, and Buy with Confidence
- Hydraulic Press Brake Troubleshooting: The Ultimate Guide to Fix Common Problems
- Press Brake Radius Mastery: Inside/Outside Radius, 8× Rule, and Real-World Tips
- Press Brake Bending Basics: Everything You Need to Know for Efficient Bending
- Everything You Need to Know About Press Brake Fundamentals