1.Introduction to fiber laser cutting technology
1.1 Brief history and development of fiber laser cutting
In modern manufacturing, there is an increasing demand for high-precision machining of extremely hard materials, and the previous cutting process has long been unable to meet the requirements of modern production. Through continuous practice and exploration, it has been discovered that fiber optic technology has excellent strength and efficiency, can achieve high-quality product design, and can be applied to a wide range of infrastructure and manufacturing applications.
Therefore, fiber laser cutting technology came into being. It originated in the 60s of the last century, with the breakthrough of fiber amplifiers, fiber laser cutting machines were manufactured and gradually played a role in the metal processing industry. In recent years, fiber laser cutting has surpassed CO₂ laser cutting technology to dominate the market as power increases and cost reductions.
1.2 Popular reasons for fiber lasers
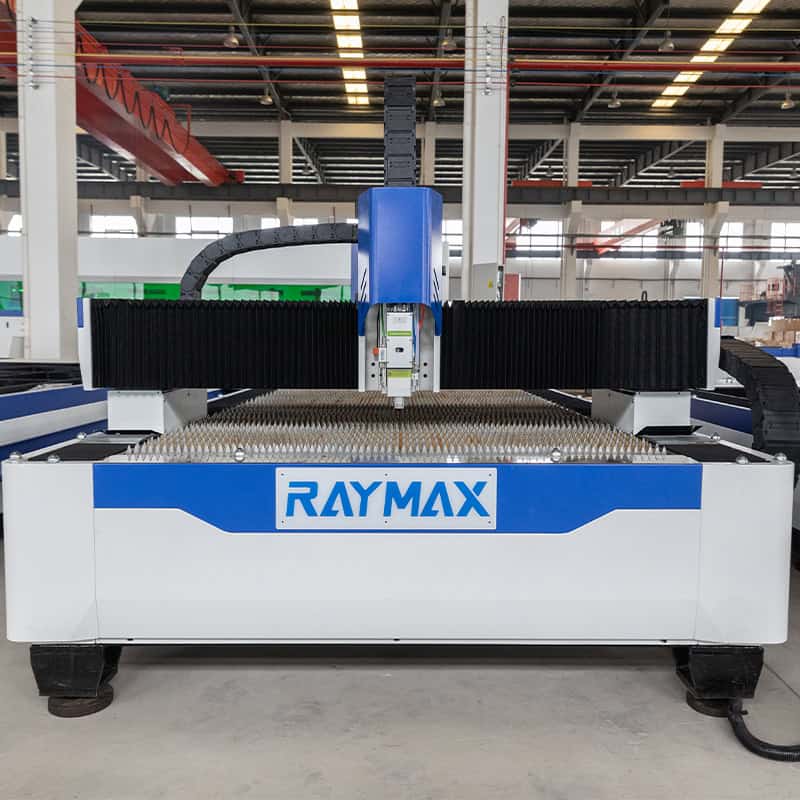
2. The core principle of fiber laser cutting machine
2.1 Interpretation of stimulus radiation
Fiber lasers produce lasers through stimulated radiation, and a large number of laser beams can precisely cut the material along a predetermined shape and path according to the instructions of the numerical control system. When cutting, energy is converted into heat energy, which melts or vaporizes the material. At this point, nitrogen or inert gas is introduced to cool the molten material and prevent oxidation, and it is blown out of the incision.
2.2 The role of optical fiber cables
Fiber optic cables are the place where high-intensity and high-precision lasers are generated and transported. In fiber optic cables, the laser is fully reflective, enabling high-quality, low-loss, long-distance transmission.
This design retains the strength of the laser and transports it, not only maintaining the accuracy and efficiency of the laser cutting, but also allowing the fiber laser cutting machine to be used in complex processing environments.
3. Key components of fiber laser cutting machine
3.1 Laser source (fiber laser generator)
The main function of a laser source is to produce a laser light. It typically uses multimode pump coupling technology with a power of 500-20kW, which means that different lasers can be generated for material cutting and manufacturing with different needs.
3.2 Cutting head (including lens and nozzle)
The cutting head contains a focusing lens and nozzle with focal lengths ranging from 5 to 7.5 inches. The focusing lens is used to concentrate the laser light into a point with a diameter of less than 0.1mm, and the nozzle is to spray the auxiliary gas to prevent the oxidation of the cut material and prevent the generation of impurities that contaminate the optical components.
3.3 Control system (numerical control system)
The control system is the “brain” of the fiber laser cutting machine, which can analyze CAD drawings and generate G code, calculate the perfect cutting path, point out specific parameters such as laser speed and rate, and ensure the accuracy of the cutting process.
3.4 Cooling system
The cooling system is undoubtedly used to cool the laser device, and the long-term work will cause the laser device to produce a thermal effect, and the use of cold water can maintain the accuracy of the machine’s production, and can also prevent damage to the overheated equipment and prolong the service life of the equipment.
3.5 Auxiliary gas system
The auxiliary gas system is closely connected to the nozzle, and the oxygen (for carbon steel), nitrogen (for stainless steel) or air (for low-cost cutting) supplied during the cutting process, with its own high pressure, prevents oxidation of the cut and ensures cutting efficiency and effectiveness.
3.6 Mechanical part
The mechanical part is usually used to move the laser beam, and is equipped with a highly rigid gantry structure, linear motor or ball screw drive system, which provides a positioning accuracy of ±0.03mm to ensure that the material can be cut into the desired shape.
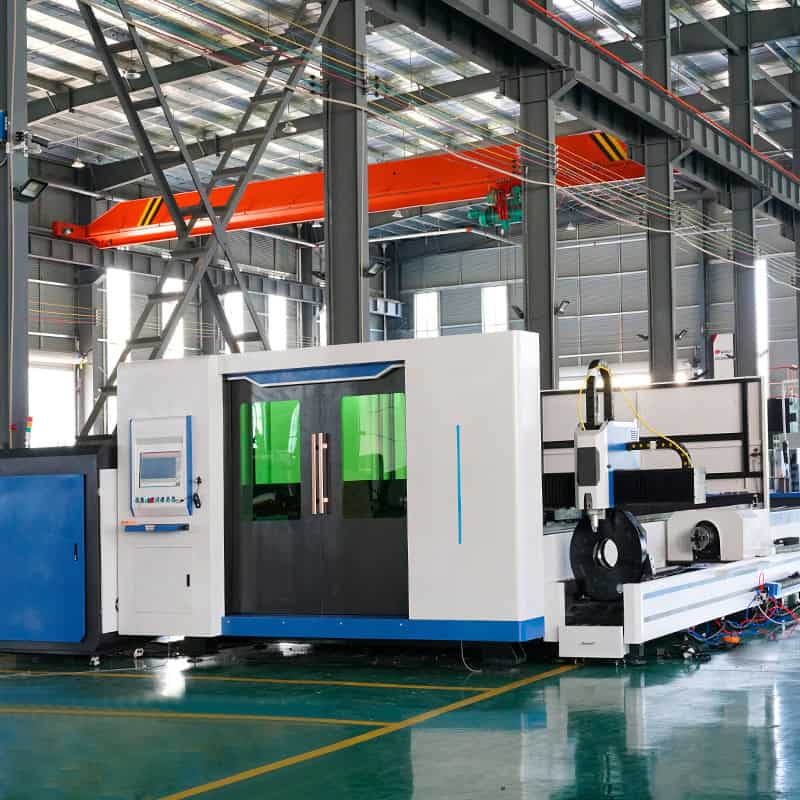
4. Step-by-step workflow of fiber laser cutting machine
4.1 Load G-code
The G-code acts as the conductor of the fiber laser cutting machine. CAD software is used to create detailed 2D or 3D models, confirm the material properties, artificially specify the size of the cut, and import the CAD file into the CAM software to determine the cutting parameters.
After completing the above steps, the CAM software will automatically generate and optimize the specific toolpath, and finally compile the path into G-code for execution.
4.2 Generation of laser beams
With a clear G-code, the pump diode excites the fiber to produce a laser light at 1064nm. The process and color of laser production may vary for different types of lasers.
4.3 Guided Laser
The optical fiber acts as a medium that transmits the resulting laser light to the cutting head.
4.4 Laser focusing
The task of the focusing system is to reduce the width of the laser beam and ensure that the laser beam is circular and free of stray light. For example, aspheric lenses can focus the beam to a diameter of 0.05-0.1 mm to achieve a highly concentrated and high-intensity cutting effect.
4.5 Material cutting
The focused beam is irradiated onto the material to be processed, and with a high power density junction and contact time of 10⁶ – 10⁷W/cm², the surface of the material heats up rapidly, is melted or vaporized, and the purpose of cutting is achieved.
4.6 Cutting head movement
The mechanical system executes the G-code instructions, controls the cutting head to move on the XY plane, and completes the cutting task according to the determined trajectory, and the moving speed will change according to the cutting complexity.
5. The main process parameters of fiber laser cutting machine
5.1 Laser power
The right laser power determines what material and how much thickness it can cut. Too little power may not be able to penetrate the material, while too much power will damage the material and reduce the quality of the cut.
5.2 Cutting speed
1mm thick carbon steel, usually the specified cutting speed is 6m/min, cutting speed is an important indicator of efficient and accurate cutting, what kind of speed depends on the thickness of the material, the size of the laser power and other parameters.
5.3 Pulse frequency
Pulse frequency refers to the number of laser pulses emitted per second. Thick plates correspond to low frequencies, which reduces material overheating; For thin plates, high frequencies are used to reduce the heat-affected zone.
5.4 Pulse duration/width
The energy and peak power of a single pulse are affected by both the pulse width and duration. The short pulse is suitable for making precision materials, heat-sensitive materials, while the long pulse is suitable for thicker materials and higher energy applications.
5.5 wavelength
The wavelength determines how the laser interacts with different materials. Fiber lasers are suitable for cutting metals, and CO2 lasers are suitable for non-metals. When processing materials, it is necessary to select the corresponding wavelength, which can optimize the material absorption rate and improve the cutting efficiency.
5.6 Focus Settings (Z-Offset Axis)
The focal length is used to focus the laser beam, and the best results are achieved by being located in the center of the thickness of the material. Proper focus alignment ensures the most efficient energy density when cutting.
5.7 Auxiliary gas types and pressures
Assist gases provide their own benefits depending on the type, oxygen to speed up the cutting of thick steel, nitrogen to prevent oxidation of stainless steel and aluminum, and compressed air to be more affordable. The pressure of the auxiliary gas can play a role in cleaning the impurities of the main equipment.
5.8 Nozzle diameter
Nozzles are used to eject an assist gas to deliver the laser, and the smaller the diameter, the higher the gas flow rate, providing a more concentrated laser.
5.9 Spacing
The distance from the nozzle to the material workpiece is called the spacing, and there is a minimum threshold for the spacing. Maintaining the spacing increases the air pressure and thus clears the cutting path.
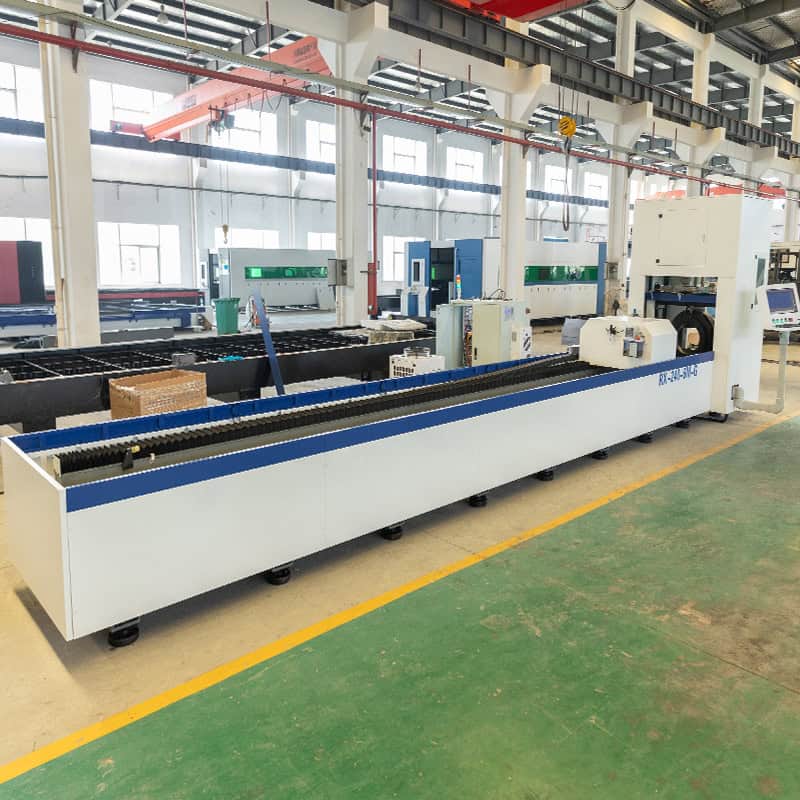
6. Advantages and disadvantages of fiber laser cutting machine
6.1 The advantages of the fiber laser cutting machine
6.2 The disadvantages of the fiber laser cutting machine
7. The difference between fiber laser and CO₂ laser cutting machine
7.1 Mechanism and Medium
Fiber laser mainly uses a solid-state gain medium to create a crystalline fiber to conduct laser; CO₂ lasers, on the other hand, use a mixture of gases to produce a laser light.
7.2 wavelengths
The wavelength ratio of fiber laser cutting machine is relatively short. So it is suitable for metallic materials and the other is suitable for non-metals.
7.3 Material and thickness applicability
The high-speed and high-precision of fiber laser is only suitable for those who are good at cutting thin metals; CO₂ lasers have the ability to cut thick plates and non-metals.
7.4 Efficiency and Output
The electrical efficiency of fiber lasers is as high as 30-50%, which is more than 2 times faster than CO₂ lasers, and the cutting speed is 2 times faster than CO₂. The high efficiency and high speed of fiber lasers are a boon for high-volume producers, while CO₂ lasers even require a ten-minute warm-up time, which can greatly reduce efficiency and yield.
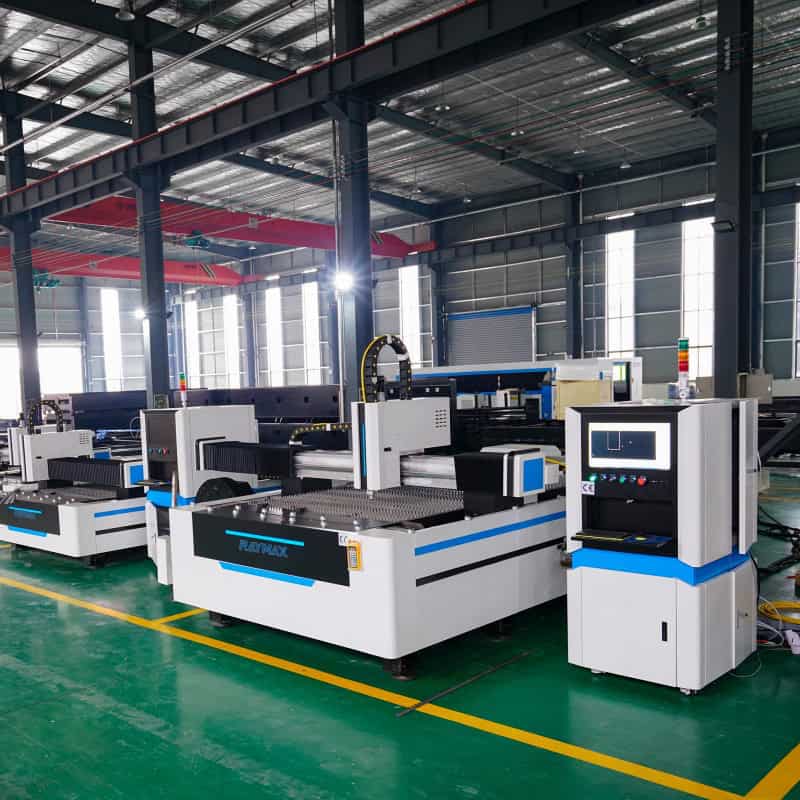
8. Application of fiber laser cutting machine
8.1 Automotive industry: It can benefit automobiles and provide many high-quality and high-precision parts for automobiles, including doors, brakes and exhaust pipes.
8.2 Aerospace: Aerospace applications require a high degree of precision, and fiber laser cutting machines are unique in the manufacture of aircraft frame components, turbine blades, and other small components.
8.3 Manufacturing: It can be seen everywhere on the assembly line of manufacturing plants, including metal processing workshops, textile mills, plastic parts, etc.
8.4 Electronic products: Electronic equipment is very demanding on the quality and accuracy of parts, and fiber laser cutting machines can manufacture parts that are consistent with them to meet most of the needs such as laptops.
8.5 Advertising: Advertising materials such as paper-cutting, signage and brand logo pay great attention to the publicity effect, which can make the advertising materials obtain smooth edges and aesthetics, and enhance the visual effect of advertising products.
8.6 Architecture: Can manufacture decorative products for the construction industry, such as cladding and art installations, etc., to increase the aesthetics of the building.
8.7 Medical: Laser power can make precision medical devices, laser surgery equipment is also popular in daily life, it provides high-quality equipment support for the medical industry.
8.8 Kitchenware industry: Many utensils in the kitchen, such as stainless steel pots, are mostly processed by fiber laser cutting machines.
8.9 Fitness equipment manufacturing: Some equipment in local gyms have strict requirements, and fiber laser cutting machines can ensure the quality and accuracy of fitness equipment.
8.10 Lighting Manufacturing: Most of the mainstream outdoor lamp pipes are formed with the help of this machine to meet the production needs of lighting equipment.
8.11 Decoration & Metal Art Manufacturing: It can be used with computer numerical control systems to create graphic designs and patterns on metal plates, make custom decorations and metal signage.
9. Conclusion
The fiber laser cutting machine converts electrical energy into laser beams, generating laser through stimulated radiation. The laser is reflected and focused within the optical fiber cable, precisely cutting and processing materials along the predetermined shape and path. With its high precision, high speed, wide adaptability, energy-saving, and low cost features, it not only enhances processing efficiency but also reduces unit costs. In modern manufacturing, it holds an important position.
Having read this, we believe you have a profound understanding of the working principle, workflow, components, process parameters, advantages and disadvantages of the fiber laser cutting machine. If you want to learn more about the knowledge of the fiber laser cutting machine, you can follow our blog news. RAYMAX, as a manufacturing enterprise of fiber laser cutting machines and press brakes, not only expands the company’s influence but also strives to provide more, more professional and comprehensive numerical control mechanical knowledge for friends in the metal processing industry. If you have any unresolved related problems or want to purchase related machines, please contact us at any time. RAYMAX offers 7*24-hour free technical support services! We look forward to your letter~~~
10. FAQ
Further Reading
10 Press Brake Bending Problems and How to Fix Them in Sheet Metal
Laser Cutting Machine application Explained: Top Materials, Applications & Safety Tips Unveiled
Choose the Right Deflection Compensation System for Accurate Bending of Long Workpieces!
The Golden Rule: How to Operate a CNC Press Brake Correctly
What is Laser Cutting Machine? The Ultimate Guide for 2025
Ultimate Guide to Hydraulic Press Brake Maintenance: Top Tools, Schedules & Expert Tips
The Ultimate Guide to Press Brake Metal Thickness
Press Brake Software: Basics, Implementation, Examples & Selection Guide
Press Brake Buyers Guide: Expert Tips to Select, Compare, and Buy with Confidence
Hydraulic Press Brake Troubleshooting: The Ultimate Guide to Fix Common Problems
Press Brake Air Bending: Guide to Principles, Calculations & Best Practices
The Complete Guide to Press Brake Techniques:11 Types of sheet metal pressing process Explained
Post Your Review
Share Your Thoughts And Feelings With Others
Hello, Customers!
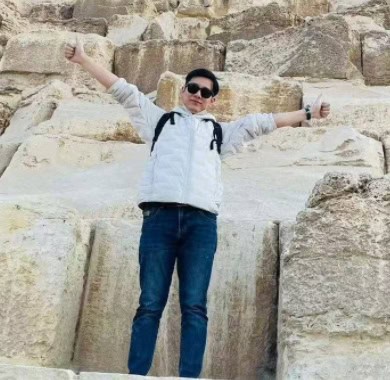
Author introduction
我叫Francis Pan,是RAYMAX的外贸经理。我从事金属制造和数控机械领域已有10多年。欢迎联系我们,我非常乐意为您提供最好的服务和产品。
邮箱: [email protected] | 微信: 13645551070
Top Guidelines
- Press Brake Air Bending: Guide to Principles, Calculations & Best Practices
- What Materials Can a Fiber Laser Cut? A Practical Handbook of Metals, Non-Metals & Limitations
- What is a Fiber Laser Cutting Machine? The Ultimate Guide for 2025
- What is Laser Cutting Machine? The Ultimate Guide for 2025
- Top 10 Fiber Laser Cutting Machine Manufacturers of 2025
- Press Brake Buyers Guide: Expert Tips to Select, Compare, and Buy with Confidence
- Hydraulic Press Brake Troubleshooting: The Ultimate Guide to Fix Common Problems
- Press Brake Radius Mastery: Inside/Outside Radius, 8× Rule, and Real-World Tips
- Press Brake Bending Basics: Everything You Need to Know for Efficient Bending
- Everything You Need to Know About Press Brake Fundamentals
One response to “The Ultimate Guide to Fiber Laser Cutting Machine Working Principles, Components, Workflow and Process Parameters”
Your writing style is captivating. A joy to read.