1. Introduction
The back gauge is a key component in the press brake. Its main function is to ensure the accurate positioning of the metal plate during the processing.The back gauge has high flexibility and can meet different processing requirements while minimizing human errors and rework rates,and also reduces material waste,thereby improving overall production efficiency.
2. What is the back gauge of the press brake
2.1 Definition and purpose of the back gauge of the press brake
The back gauge of the press brake is a mechanical system and a key tool in the metal processing industry.It is mainly used for accurate workpiece positioning to ensure the accuracy of the bending work of the metal sheet.Its purpose is to ensure that each bend can meet the bending requirements and reduce the rework rate caused by errors.
2.2 Core functions and importance of press brake operation
The core function of the back gauge is that it can be quickly and accurately reset and coordinated with other parts of the machine to better match different thicknesses and material types.The accuracy and flexibility of the back gauge can also help us greatly improve the bending production efficiency and ensure the quality of the finished workpiece.
3. Types of back gauges
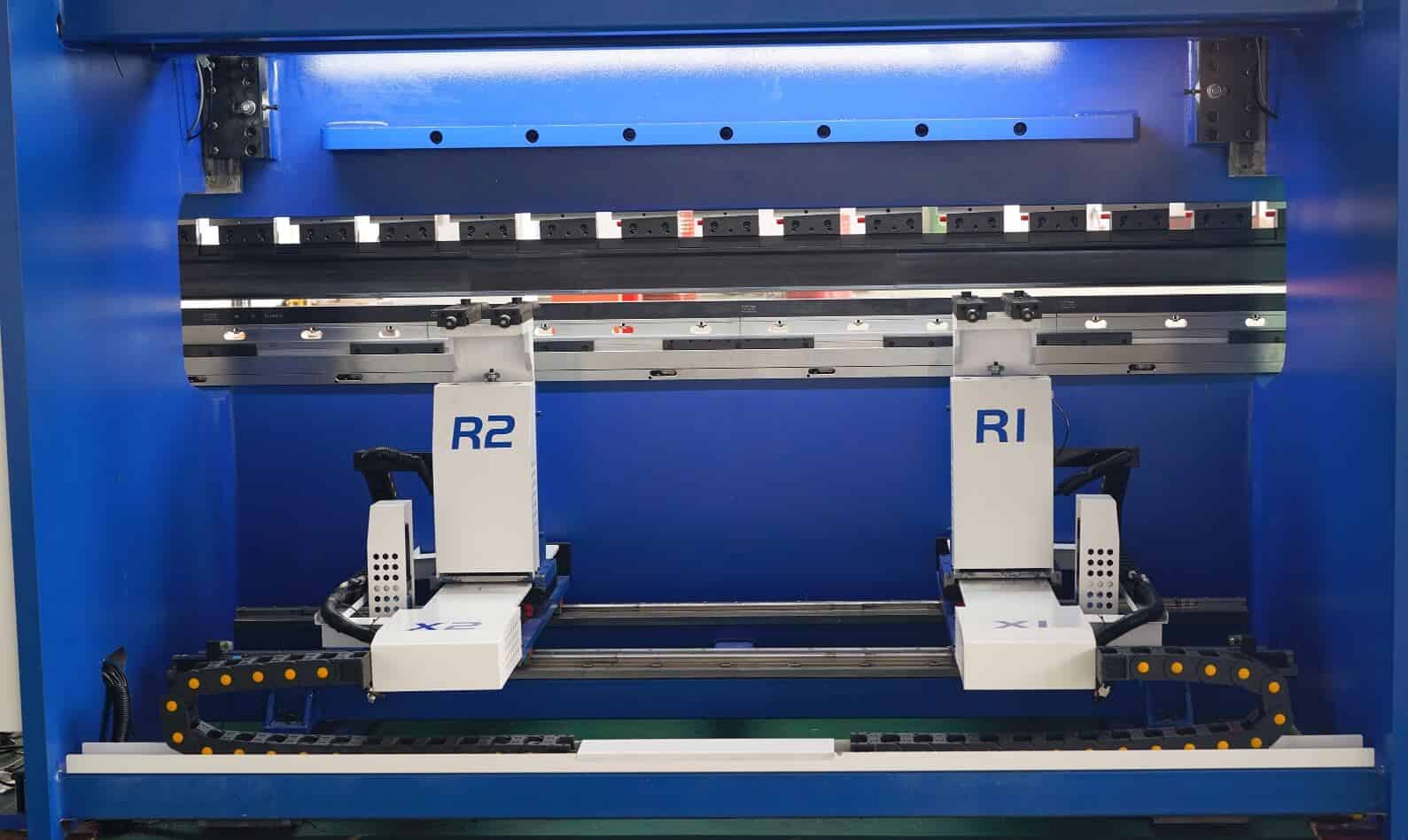
3.1 Manual press brake back gauge
The manual brake press back gauge is the simplest type of back gauge in the press brake bending machine.As the name implies,it is a type of back gauge that is completely manually operated by the operator.Therefore,the whole process is relatively time-consuming and labor-intensive.The advantage is that the budget is sufficient.Because this type of back gauge is affordable,it is mostly used in small workshops,especially in prototype bending processing occasions where the number of bends is relatively small.
3.2 CNC press brake back gauge
The CNC back gauge is controlled by a computer,and the instructions are sent to the back gauge operation through precise calculations,which ultimately forms a repeatable and high-precision bending operation.The CNC press brake back gauge is suitable for working environments with large-scale production,high efficiency and relatively complex bending requirements.Such as:processing of automotive sheet metal parts.
In addition,the CNC brake press back gauge is divided into three types:single-axis,double-axis and multi-axis:
3.3 Robot backgauge
Because the robot backgauge uses advanced bending technology to locate and handle the workpiece,it also makes the bending work more automated.It is more suitable for high-speed and high-precision bending work,such as the automotive and aerospace industries or large-scale production.
3.4 Wireless press brake backgauge
The operation of the wireless brake press backgauge is more flexible.It is remotely programmed and controlled through a wireless network,and it also allows the operator to work in a freer space,so it is more suitable for more complex and changeable working environments,such as large manufacturing workshops or handling oversized materials.
3.5 Function and Application Comparison
Different types of back gauges have different effects in terms of functions and usage scenarios.When purchasing a system,we can combine actual needs and choose the appropriate back gauge,which can also help us improve production efficiency and production accuracy.
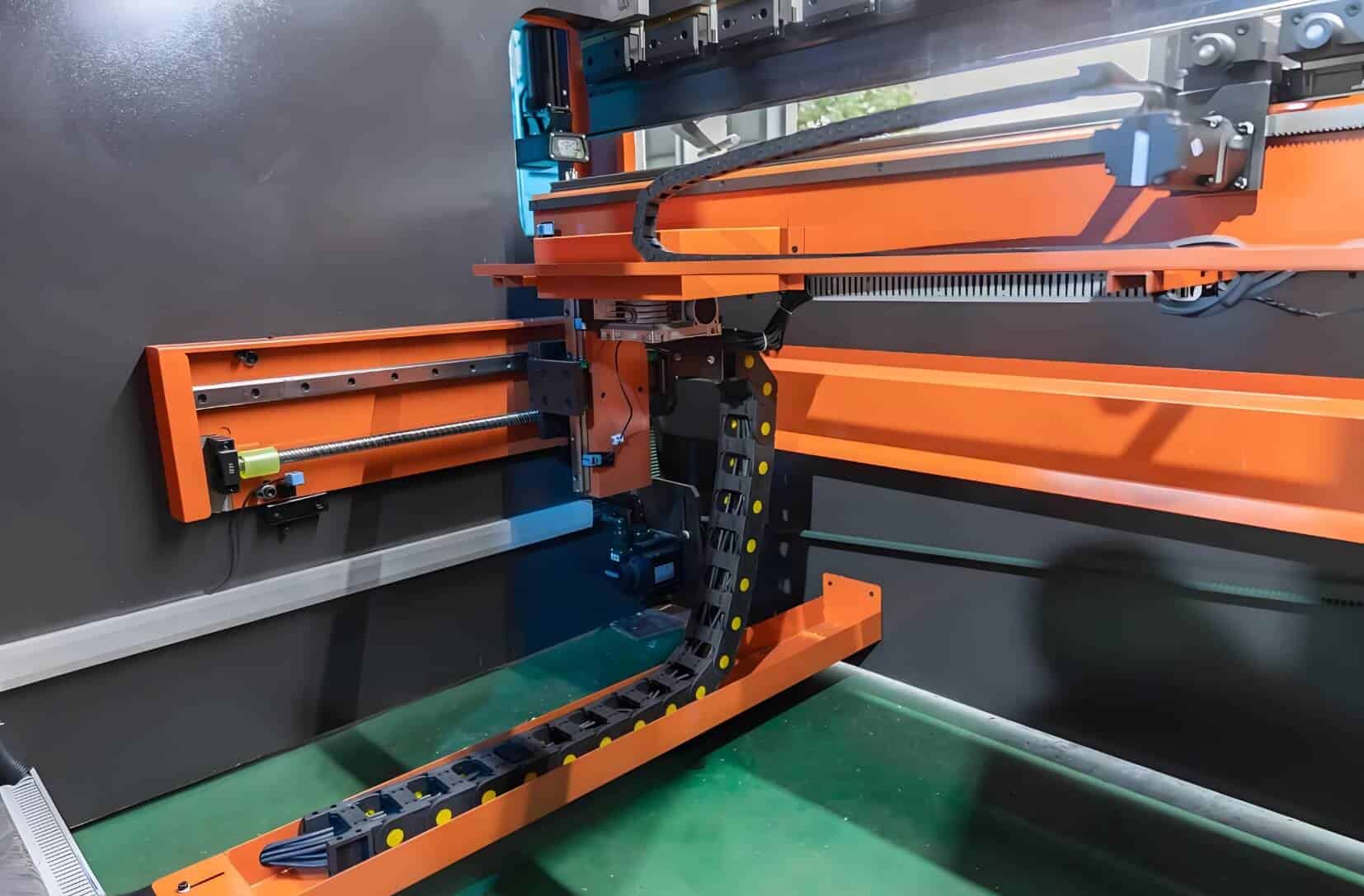
4. Key components of the back gauge system
4.1 Crossbeam
The crossbeam is a key component of the back gauge system.It provides vital support and calibration for other components of the back gauge system.In order to ensure stability and rigidity during the bending process,the crossbeam is generally forged from high-strength steel,which also improves the processing accuracy to a certain extent.
4.2 Screw mechanism
The screw mechanism is the movement mechanism of the back gauge,which can convert rotational motion into linear motion with minimal friction.The accuracy of the screw is an important factor affecting the overall performance of the press brake bending machine,which ensures the consistency and accuracy of each bend.
4.3 Engine(motor)
The engine is also called a motor,which is responsible for driving the movement of the back gauge.These motors provide torque and speed control for the back gauge,helping the back gauge to achieve precise positioning.These systems generally have high response speed and stability,and can basically meet the requirements of high-precision work.
4.4 Stopper claws and blocks
The stopper claws and blocks directly contact the workpiece and are generally installed on the back gauge.They can also be adjusted to different positions to match different bending sizes.The stopper claws and blocks can withstand repeated use and can ensure the stability of the workpiece during the bending process.
4.5 Guide rails and sliders
The correct calibration and maintenance of the guide rails are crucial for the back gauge.Its smooth and precise movement can provide a stable path,which can ensure that the back gauge can slide smoothly during adjustment and operation,and reduce friction and wear to a certain extent.
4.6 Mechanism and motion
The motion mechanism of the back gauge is driven by a motor,and the power is transmitted to the lead screw through the motor.The coordinated combination of the motor,lead screw and guide rails can ensure that the back gauge can accurately position the workpiece in each bending operation,greatly improving the response speed,accuracy and durability during the work process.
4.7 Axis and Control
The control mechanism of the back gauge system is to feedback real-time data through sensors and control devices.The back gauge of a modern press brake can control operations on multiple axes to ensure accurate positioning of the workpiece.
5. The importance of using a back gauge
The importance of using a back gauge includes many aspects,such as:
Its flexibility and versatility allow it to adapt to market demand more quickly;
The automation of the back gauge of a press brake bending machine can simplify the production process and shorten the time setting,thereby greatly improving productivity and efficiency;
The sensors and measurement systems in the back gauge are also advanced enough to adjust some subtle changes in real time,which can greatly improve precision and accuracy,minimize errors and material waste,and improve the quality of the final product;
The precise setting of the back gauge also reduces many safety hazards caused by improper operation,providing a safer working environment for the operator.
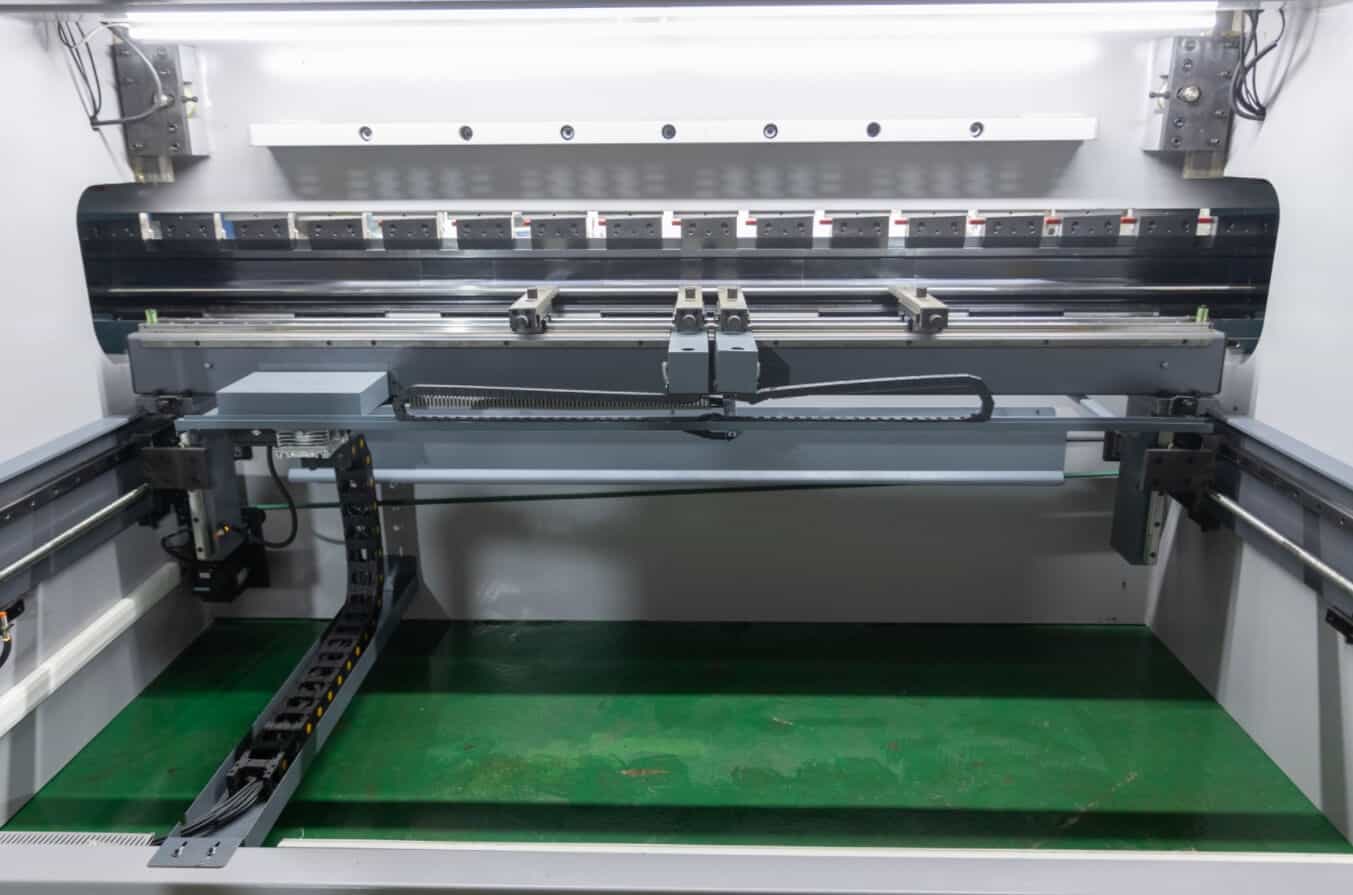
6. Calibration and maintenance of the back gauge of a press brake
6.1 Steps for back gauge calibration
The steps for back gauge calibration are:check the equipment status;connect the measuring tool;adjust the position of the back gauge.
6.2 Back gauge maintenance guide
Back gauge maintenance includes daily,weekly and monthly regular inspections and clearances,lubrication of lead screws and guide rails,detection of motor operation and component functions,removal of debris and keeping moving parts flexible.
6.3 Back gauge calibration frequency
The number of back gauge calibrations can be planned according to the frequency of use and the type of material.In order to ensure a stable working state,we can calibrate once a week or month.
7. Common problems and solutions
7.1 The main purpose of the back gauge of the press brake
The main function of the back gauge of the brake press is to ensure the accuracy of the metal processing process,thereby improving the repetitive accuracy of the bending.
7.2 What are the differences between the back gauges of different types of press brakes?
Different types of press brake back gauges have obvious differences in control systems,accuracy,speed and degree of automation.We must choose the appropriate back gauge of the press brake according to the actual situation.
7.3 How to calibrate the back gauge of the press brake
Repeatedly adjust according to the calibration steps mentioned in the above content of this article.
7.4 Common problems and solutions for the back gauge of the press brake
Common problems include inaccurate positioning,component wear and poor movement.These can be solved by regular inspection and calibration,replacement of damaged parts,etc.
7.5 Best practices for optimizing the efficiency of the back gauge of the brake press
Choosing the right back gauge for the brake press,improving the operator’s work enthusiasm,and continuously optimizing the program are all ways to optimize efficiency.
8. Conclusion
Seeing this,I believe you have a certain understanding of the definition of the back gauge of the press brake and how to select it.If you are considering buying a press brake bending machine with a back gauge system,I hope the above content can help you the most.In addition,if you are still not sure which press brake model is suitable for you,you can choose to contact us directly.RAYMAX’s technicians are online 7*24 hours a day to provide you with free technical services! I am Francis,and I am committed to quickly providing you with helpful professional knowledge in the field of CNC machinery!
Further Reading
The Ultimate Guide to Fiber Laser Cutting Machine Working Principles, Components, Workflow and Process Parameters
Ultimate Guide to Press Brake Punches: Eleven Types, Materials, Selection, and Maintenance
The top 10 best press brake manufacturers in the world in 2025
Press Brake Radius Mastery: Inside/Outside Radius, 8× Rule, and Real-World Tips
Press Brake Buyers Guide: Expert Tips to Select, Compare, and Buy with Confidence
Metal Laser Cutting Machine: Buyer’s Ultimate Guide to Costs, Types & Quality Factors
What Materials Can a Fiber Laser Cut? A Practical Handbook of Metals, Non-Metals & Limitations
How Does an Electric Press Brake Work? Working Principle, Core Parts and Pros
One Article to Master CNC Press Brakes: Types, Workflow, Structure & Buying Tips
What is Laser Cutting Machine? The Ultimate Guide for 2025
The Ultimate Guide to Press Brake Safety Devices and Guidelines for 2025
What Is a Tandem Press Brake? Benefits, Applications & Buying Tips
Post Your Review
Share Your Thoughts And Feelings With Others
Hello, Customers!
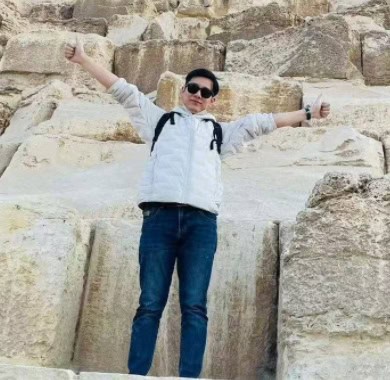
Author introduction
我叫Francis Pan,是RAYMAX的外贸经理。我从事金属制造和数控机械领域已有10多年。欢迎联系我们,我非常乐意为您提供最好的服务和产品。
邮箱: [email protected] | 微信: 13645551070
Top Guidelines
- Press Brake Air Bending: Guide to Principles, Calculations & Best Practices
- What Materials Can a Fiber Laser Cut? A Practical Handbook of Metals, Non-Metals & Limitations
- What is a Fiber Laser Cutting Machine? The Ultimate Guide for 2025
- What is Laser Cutting Machine? The Ultimate Guide for 2025
- Top 10 Fiber Laser Cutting Machine Manufacturers of 2025
- Press Brake Buyers Guide: Expert Tips to Select, Compare, and Buy with Confidence
- Hydraulic Press Brake Troubleshooting: The Ultimate Guide to Fix Common Problems
- Press Brake Radius Mastery: Inside/Outside Radius, 8× Rule, and Real-World Tips
- Press Brake Bending Basics: Everything You Need to Know for Efficient Bending
- Everything You Need to Know About Press Brake Fundamentals