1. Regarding the accuracy issue of bending long workpieces
Press brakes are indispensable tools in metal processing. Their function is to bend metal sheets into various pre-set shapes. Among them, when we use press brakes to bend long workpieces, the workpieces often have a large bending angle in the middle and a small angle at both ends. We call this situation “deflection”. Therefore. The necessary deflection compensation work is a crucial step to achieve consistent bending angles.
2. Deflection phenomenon and its impact during bending
2.1 The phenomenon of concave slide and middle of workbench due to force during bending
When we use press brakes to bend, the pressure applied may cause the slide and middle of the workbench of the machine to concave. This problem becomes more obvious when we deal with long and thick parts. It will increase the gap between the press brake tools, resulting in a more “open” bending angle in the middle and a more “sharp” bending angle at both ends.
2.2 Practical problems caused by deflection
Deflection brings many practical problems, such as uneven bending angles. Due to the influence of deflection, the bending angle of the workpiece is inconsistent in length, which results in the inability of the produced parts to match the design requirements. Another example is the product size error. Deflection will produce obvious dimensional deviations, increase the probability of rework and scrap, and reduce production efficiency.
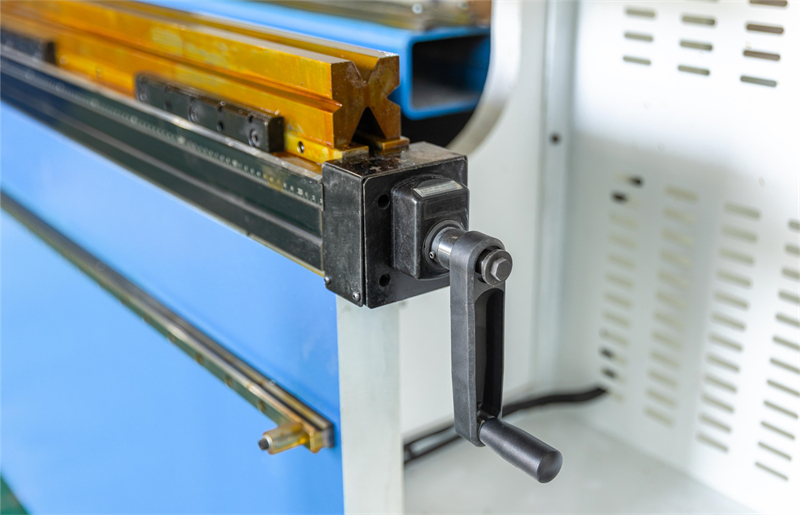
3. What is deflection compensation
3.1 Definition of deflection compensation technology
Deflection compensation is a technology used to offset the extrusion deformation of long workpieces caused by the press brake worktable and slider due to force. The principle is to actively adjust the curvature of the press brake worktable or slider before bending, thereby offsetting the bending pressure, and finally ensuring that the bending angle of the long workpiece is consistent.
3.2 Basic working principle of deflection compensation
When the machine is working, the compensation system will automatically adjust so that the worktable is moderately “convex” in the opposite direction of the actual bending deformation. It can ensure that the error caused by deformation is effectively avoided during the entire bending process.
4. Types and comparisons of deflection compensation systems
4.1 Hydraulic compensation system
The working principle of the hydraulic compensation system is to apply pressure through the cylinder to partially raise the worktable, which can offset the deflection in the middle. It can be adjusted automatically and has a wider range of applications; however, the maintenance cost is relatively high, and the cleanliness of the hydraulic system is required to be higher.
4.2 Mechanical compensation system
The mechanical compensation system uses a mechanical device to adjust the shape of the workbench. It has a simple structure and good long-term stability; however, it has poor flexibility, requires manual parameter setting, and has a low degree of automation.
4.3 Electric compensation system
The working principle of the electric compensation system is to rely on motor adjustment. It is usually combined with a modern CNC system and has a high degree of automation. The electric compensation system can not only achieve dynamic adjustment compensation, but also data traceability; however, its cost is relatively high and the initial investment is large.
4.4 Comparative analysis of various compensation methods
Different systems have their own characteristics and advantages and disadvantages in terms of cost, maintenance requirements, and material processing capabilities. When choosing, we should decide according to different application scenarios. For example, hydraulic compensation systems are widely used in medium and thick plates; mechanical compensation systems are suitable for high-precision large-piece bending; electric compensation systems are widely used in intelligent manufacturing and automatic production lines.
For a more detailed introduction to deflection compensation technology, please refer to: Crowning System
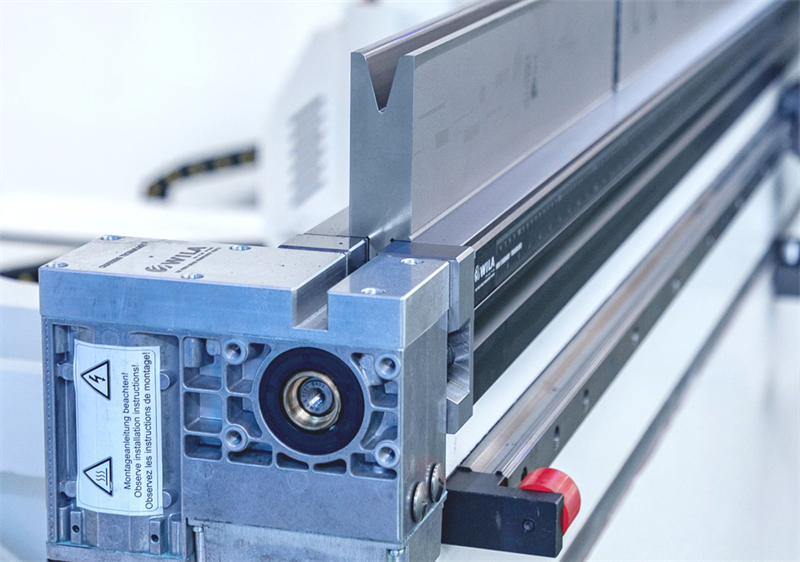
5. Benefits of a deflection compensation system
5.1 Improve bending accuracy and ensure the consistency of finished products
The compensation system eliminates deflection to increase the matching degree between products, make the angle of each bending line consistent, minimize the bending tolerance, and thus improve the overall quality of the finished bending products.
5.2 Reduce material waste and rework rate
The compensation system can prevent defects such as bending or twisting, and minimize the need for rework. Accurate bending operations can reduce material waste caused by dimensional incompatibility and reduce rework rates.
5.3 Improve production efficiency and yield rate
The compensation system optimizes the bending process, reduces manual adjustment and downtime maintenance time, and effectively improves the operation speed and yield rate of each process.
5.4 Possible labor cost savings
Not only does it reduce the need for rework and material waste, but it can also significantly save labor costs, thereby reducing production costs.
6. Advantages of modern deflection compensation technology
6.1 Linkage between CNC system and compensation system
Modern CNC press brakes can automatically control the compensation system, realizing the linkage between parameter setting and real-time adjustment. Ensure the accuracy of bending and improve production efficiency.
6.2 The impact of increasing the degree of automation
The intelligent compensation system greatly reduces the involvement of human labor, which not only improves the accuracy of operation, but also reduces the impact of human factors on production efficiency and product quality.
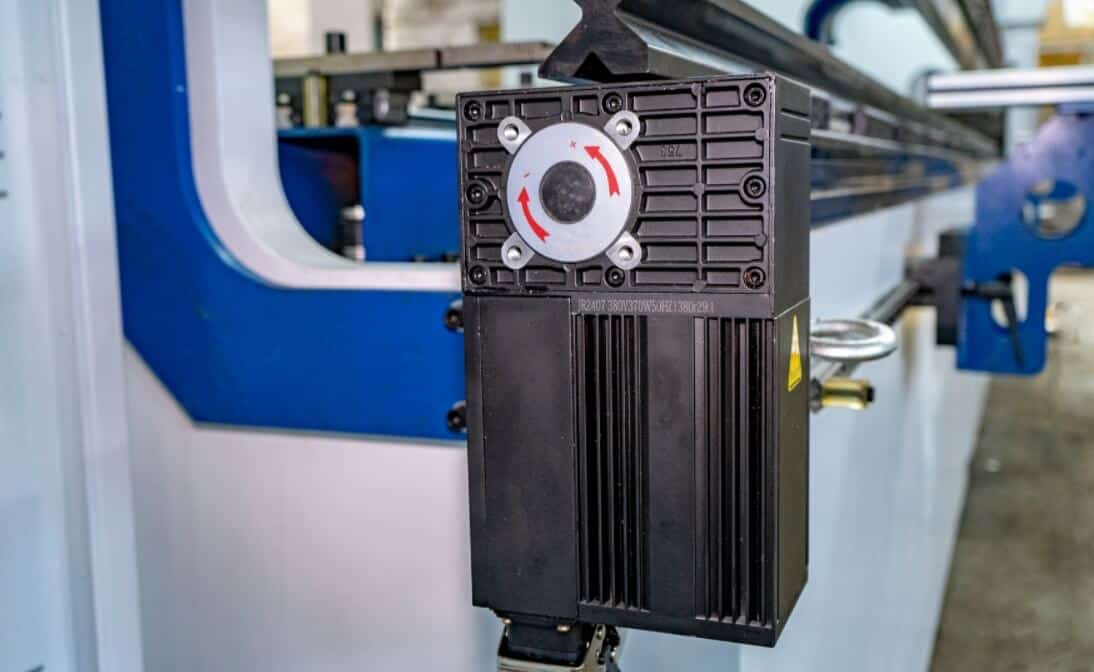
7. Suggestions for purchasing press brake deflection compensation system
7.1 Choose the appropriate compensation method according to processing requirements and product type
Due to the different requirements of different materials and products, we should consider the applicability of the machine when choosing the compensation method. For example, thick plates produced in batches are suitable for hydraulic compensation systems, while special high-precision long workpieces are more suitable for mechanical compensation systems.
7.2 Key parameters and configurations that need attention
When purchasing a compensation system, we should focus on factors such as the accuracy, response speed and maintenance complexity of the compensation system, which will affect our use.
7.3 The importance of consulting professional manufacturers and service providers
Listening to the opinions of industry experts and obtaining professional services can help us choose the most suitable compensation system and solution, reduce investment costs and risks, and greatly improve production efficiency.
8. Conclusion
Adopting a reasonable and perfect deflection compensation system can not only improve production efficiency and product quality, but also reduce various production costs, which is an important factor in improving enterprise competitiveness.
Further Reading
Press Brake Air Bending: Guide to Principles, Calculations & Best Practices
10 Press Brake Bending Problems and How to Fix Them in Sheet Metal
What is Laser Cutting Machine? The Ultimate Guide for 2025
Press Brake Software: Basics, Implementation, Examples & Selection Guide
What is a Fiber Laser Cutting Machine? The Ultimate Guide for 2025
Press Brake Bending Basics: Everything You Need to Know for Efficient Bending
One-Stop Guide to Hydraulic Press Brake: Working Principle, Bending Process & Applications
Metal Laser Cutting Machine: Buyer’s Ultimate Guide to Costs, Types & Quality Factors
NC vs CNC Press Brake: Key Differences, Selection Guide, and Industry Applications
What Materials Can a Fiber Laser Cut? A Practical Handbook of Metals, Non-Metals & Limitations
CNC Press Brake Axis: Mastering Configurations from 2-Axis to 8+1 for Pro Results
Definition of press brake tool material
Post Your Review
Share Your Thoughts And Feelings With Others
Hello, Customers!
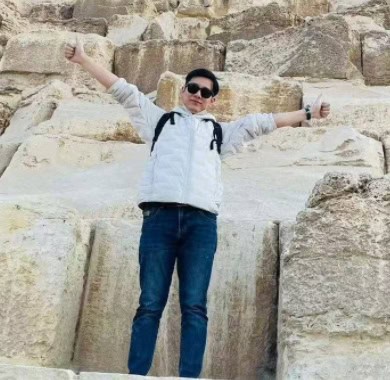
Author introduction
我叫Francis Pan,是RAYMAX的外贸经理。我从事金属制造和数控机械领域已有10多年。欢迎联系我们,我非常乐意为您提供最好的服务和产品。
邮箱: [email protected] | 微信: 13645551070
Top Guidelines
- Press Brake Air Bending: Guide to Principles, Calculations & Best Practices
- What Materials Can a Fiber Laser Cut? A Practical Handbook of Metals, Non-Metals & Limitations
- What is a Fiber Laser Cutting Machine? The Ultimate Guide for 2025
- What is Laser Cutting Machine? The Ultimate Guide for 2025
- Top 10 Fiber Laser Cutting Machine Manufacturers of 2025
- Press Brake Buyers Guide: Expert Tips to Select, Compare, and Buy with Confidence
- Hydraulic Press Brake Troubleshooting: The Ultimate Guide to Fix Common Problems
- Press Brake Radius Mastery: Inside/Outside Radius, 8× Rule, and Real-World Tips
- Press Brake Bending Basics: Everything You Need to Know for Efficient Bending
- Everything You Need to Know About Press Brake Fundamentals